图书介绍
现代模具设计基础【2025|PDF|Epub|mobi|kindle电子书版本百度云盘下载】
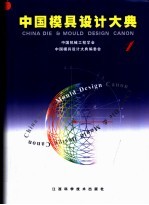
- 中国机械工程学会,中国模具设计大典编委会 著
- 出版社: 南昌:江西科学技术出版社
- ISBN:7539019484
- 出版时间:2003
- 标注页数:1085页
- 文件大小:90MB
- 文件页数:1106页
- 主题词:
PDF下载
下载说明
现代模具设计基础PDF格式电子书版下载
下载的文件为RAR压缩包。需要使用解压软件进行解压得到PDF格式图书。建议使用BT下载工具Free Download Manager进行下载,简称FDM(免费,没有广告,支持多平台)。本站资源全部打包为BT种子。所以需要使用专业的BT下载软件进行下载。如BitComet qBittorrent uTorrent等BT下载工具。迅雷目前由于本站不是热门资源。不推荐使用!后期资源热门了。安装了迅雷也可以迅雷进行下载!
(文件页数 要大于 标注页数,上中下等多册电子书除外)
注意:本站所有压缩包均有解压码: 点击下载压缩包解压工具
图书目录
第1篇 模具计算机辅助设计3
第1章 概论3
1 计算机辅助设计(CAD)的基本概念3
2 CAD在模具设计中的应用4
2.1 计算机在设计过程中的辅助作用4
2.2 模具CAD/CAM技术的应用5
2.3 模具CAD的优越性6
2.4 模具CAD的特点6
3 传统的模具设计制造与模具CAD/CAM的比较7
3.1 传统模具设计与制造7
3.2 集成的模具设计制造流程7
1.2 外部存储器9
1.1 主机9
1 模具CAD系统的硬件9
第2章 模具CAD系统的组成9
1.3 输入设备10
1.4 输出设备11
2 计算机网络14
3 模具CAD系统的软件16
3.1 系统软件16
3.2 支撑软件16
3.3 应用软件18
第3章 模具CAD中的数据处理19
1 常见的数据结构19
1.1 数据结构19
1.2 常用的数据结构20
2.1 以数组的形式存放数表23
2 数表的处理方法23
2.2 以数据文件形式存放数表24
2.3 函数插值方法25
2.4 交互处理方法26
3 线图的程序化26
4 建立经验公式的方法27
4.1 处理数表的回归分析方法27
4.2 多项式拟合28
4.3 线性拟合与可化为线性拟合的问题28
第4章 模具CAD的图形技术基础30
1 图形的变换30
1.1 二维图形的变换30
1.2 三维图形的变换32
1.3 透视变换35
2 交互技术36
2.1 交互输入技术37
2.2 用户界面设计37
第5章 CAD的建模技术40
1 几何造型的基本概念40
1.1 形体的信息结构40
1.2 布尔运算40
1.3 欧拉公式41
2 形体的表示模式41
2.1 体素调用表示41
2.2 空间点列表示41
2.3 单元分解表示41
2.7 混合模式42
2.6 边界表示(B-Reps)42
2.4 扫描变换表示42
2.5 构造体素表示(CSG)42
3 用于模具CAD几何建模系统的功能43
3.1 几何造型系统功能43
3.2 模具CAD理想的几何造型系统特点44
4 参数曲线与曲面建模45
4.1 贝赛尔(Bezier)曲线与曲面45
4.2 B样条曲线和曲面46
4.3 非均匀有理B样条(NURBS)曲线与曲面47
5 参数化特征建模49
5.1 特征建模技术49
5.2 参数化技术51
5.3 参数化特征造型的基本方法54
6 装配建模技术55
6.1 装配建模的基本概念55
6.2 装配建模的一般方法57
6.3 基于功能组件的模具装配设计方法58
第6章 产品数据管理(PDM)技术60
1 PDM技术概述60
1.1 PDM技术产生的背景60
1.2 PDM的定义60
1.3 PDM系统的体系结构60
2 PDM系统的功能61
2.1 数据与文档管理61
2.3 产品结构与配置管理63
2.4 零部件分类库管理63
2.2 过程与工作流程管理63
2.5 项目管理64
2.6 其他功能64
3 PDM系统的实施64
3.1 PDM实施的内容64
3.2 PDM实施的基本步骤65
3.3 PDM的信息建模65
3.4 成功实施PDM应注意的几个问题68
4 基于PDM的系统集成68
4.1 基于PDM实现应用集成的三个层次68
4.2 模具CAD/CAPP/CAM与PDM的集成69
2 冲裁件工艺性判断71
1 冲裁模CAD/CAM系统的结构与功能71
第7章 冲裁模CAD71
2.1 判别模型的建立73
2.2 处理图形的几种算法73
2.3 工艺性的自动判别过程74
3 毛坯优化排样75
3.1 毛坯排样问题的数学描述75
3.2 多边形法76
3.3 高度函数法76
3.4 平行线分割纵横平移法78
4 冲裁工艺方案的设计80
4.1 模具类型的选择80
4.2 连续模的工步设计82
5.1 冲裁模结构设计子系统的功能结构84
5 冲裁模结构设计84
5.2 总装图设计85
5.3 凹模与凸模设计85
第8章 级进模CAD88
1 级进模设计内容及过程分析88
2 级进模CAD系统的结构与功能89
2.1 系统的总体结构89
2.2 功能模块组成90
3 基于特征的冲压工艺设计91
3.1 板金零件的单元特征模型91
3.2 基于特征的冲压工艺设计方法93
4.1 级进模结构的装配模型96
4 级进模结构与零件CAD96
4.2 总体结构及零件设计97
第9章 覆盖件模具CAD100
1 覆盖件模具CAD系统结构100
1.1 冲压工艺设计100
1.2 模具结构设计100
2 覆盖件模具冲压工艺CAPP101
2.1 冲压工艺CAPP系统的总体结构101
2.2 覆盖件冲压工艺的数据库管理系统102
2.3 基于成组技术的检索式工艺设计106
3 基于特征的冲压工序详细设计107
3.1 覆盖件产品的分类描述方法107
3.2 拉延工序件设计107
4.1 基于典型结构的覆盖件模具结构二维设计111
4 覆盖件模具结构设计111
4.2 基于特征的覆盖件模具结构三维设计113
第10章 注塑模CAD115
1 注塑模CAD/CAE/CAM概述115
1.1 塑料模CAD/CAM的发展115
1.2 塑料模CAD/CAM系统的工作流程115
2 注塑模CAD的内容及特点117
2.1 注塑模结构CAD的内容117
2.2 注塑模CAD的特点118
3 注塑模CAD软件的开发118
3.1 软件结构119
3.2 标准模架选择及编码119
3.3 镶拼式模具结构设计120
4.1 流道系统的结构122
4 注塑模流道系统的设计122
4.2 流道系统的设计计算123
第11章 锻模CAD127
1 利用成组技术建立锻模CAD系统的方法127
2 锻件与毛坯形状复杂性的定量计算130
3 轴对称件锻模CAD系统131
3.1 轴对称件锻模CAD/CAM系统的组成131
3.2 轴对称锻件几何形状的输入132
3.3 锻件设计132
3.4 锻模设计133
4 长杆类锻模CAD系统133
4.1 长杆类锻模CAD/CAM系统的总体结构133
4.2 模锻工艺设计134
4.3 拔长型槽的设计135
4.4 滚挤型槽的设计137
4.5 型槽的布置138
5 飞边槽尺寸和飞边金属消耗的计算140
5.1 计算飞边槽桥部尺寸的算法140
5.2 计算飞边金属消耗的算法140
6 预锻型槽的设计141
6.1 预锻型槽的设计规则141
6.2 预锻型槽截面的设计方法142
参考文献143
1 连续介质的运动与变形149
1.2 张量基础149
1.1 连续介质力学的基本概念149
第1章 材料成形分析的理论基础149
第2篇 材料成形过程的数值模拟149
1.3 变形几何学153
1.4 运动学156
2 应力157
2.1 体力和面力157
2.2 柯西应力张量158
2.3 其他应力张量158
2.4 应力速率159
3 基本方程和原理160
3.1 基本方程160
3.2 边值问题与初值问题161
3.3 虚功原理与虚功率原理162
4.1 本构关系的一般原理163
4 本构方程163
4.2 弹性本构方程164
4.3 弹塑性本构方程164
4.4 黏塑性本构方程170
4.5 塑性细观力学本构关系172
4.6 流体的本构方程176
4.7 热传导问题178
4.8 状态方程178
第2章 有限元法基础180
1 引言180
2 加权余量法与变分法181
2.1 加权余量法181
2.3 弹性力学中的变分原理182
2.2 变分原理和里兹法182
2.4 约束变分原理184
3 有限元法的实施步骤185
3.1 单元分析185
3.2 实施步骤190
3.3 收敛准则和解的性质190
4 单元模型191
4.1 二维问题191
4.2 轴对应问题195
4.3 三维问题196
4.4 等参单元199
4.5 结构单元203
4.6 单元模型小结211
5.1 线性方程组的求解221
5 有限元方程的求解221
5.2 非线性方程组的求解223
6 有限元前后置处理224
6.1 有限元法模型化和前置处理224
6.2 后置处理228
6.3 利用CAD/CAM的交互式图形界面229
第3章 刚塑性有限元法230
1 刚塑性变分原理230
1.1 刚塑性材料的边值问题230
1.2 理想刚塑性材料的变分原理231
1.3 刚塑性材料不完全广义变分原理231
2.1 离散化233
2 刚塑性有限元公式233
2.2 有限元求解公式236
2.3 刚塑性有限元模拟分析步骤237
3 刚黏塑性有限元法238
3.1 黏塑性材料的变分原理238
3.2 刚黏塑性有限元公式239
4 计算中的几个问题240
4.1 刚性区的处理240
4.2 初始速度场的生成240
4.3 迭代收敛判据242
4.4 摩擦边界条件242
4.5 动态接触边界条件的处理244
4.6 网格重新划分247
1.1 应力应变矩阵249
第4章 弹塑性有限元静力分析249
1 小变形弹塑性有限元法249
1.2 增量形式的虚功原理250
1.3 有限元方程250
1.4 求解步骤251
2 有限应变弹塑性有限元分析252
2.1 应力应变矩阵253
2.2 虚功率方程253
2.3 有限元方程254
3 有限元逆算法256
3.1 理想形变理论256
3.2 有限元逆算法256
3.3 有限元逆算法应用实例257
第5章 有限元动力分析260
1 动力分析的有限元方程260
1.1 一维动力系统260
1.2 虚功率方程和有限元方程261
2 显式时间积分方法263
2.1 中心差分法263
2.2 时间步长的确定263
2.3 动力显式算法的进一步讨论264
3 隐式时间积分方法265
3.1 Newmark法265
3.2 显式与隐式算法的比较和显隐结合的方法266
1.2 建立有限元分析模型268
1.1 建立几何模型268
1 塑性成形模拟的一般步骤268
第6章 塑性成形模拟的实施268
1.3 定义工具和边界条件270
1.4 求解270
1.5 后处理270
1.6 CAE与CAD的集成270
2 工具加载的模型化271
2.1 工具与制件之间的接触271
2.2 拉延肋阻力模型275
3 热分析与热力耦合分析276
3.1 热传导问题的基本方程276
3.2 稳态温度场的有限元法277
3.3 瞬态温度场的有限元法278
3.4 变形与传热过程的藕合分析279
3.5 热力耦合分析的基本方程280
3.6 热力藕合分析的有限元法281
4 组合性能的变化和成形缺陷预测282
4.1 塑性成形过程中材料组织性能的变化282
4.2 成形缺陷预测282
第7章 塑性成形数值模拟的应用实例286
1 锻造过程的数值模拟286
1.1 尾轮锻造286
1.2 曲轴RR弯曲镦锻287
2 挤压过程的数值模拟289
3.1 逆算法的应用290
3.2 增量法的应用290
3 冲压过程的数值模拟290
第8章 有限差分法295
1 差分的基本原理及逼近误差295
1.1 差分原理295
1.2 逼近误差296
2 差分方程、截断误差和相容性298
2.1 差分方程298
2.2 截断误差299
2.3 相容性300
3 收敛性与稳定性300
3.1 收敛性300
3.2 稳定性302
4 Lax等价定理304
1.1 傅里叶定律306
1.2 三维热传导微分方程306
第9章 温度场分析306
1 数学模型306
2 数值求解方法307
2.1 有限差分法(FDM)307
2.2 直接差分法(DFDM)308
2.3 改值的直接差分方程310
2.4 直接差分法(DFDM)与有限差分法(FDM)比较311
3 初始条件311
4 边界条件311
4.1 热传导边界条件312
4.2 热辐射边界条件312
5.2 考虑析出潜热的热能守恒式313
5.1 定义313
5 潜热处理313
4.4 液体金属和凝固层、铸锭和铸型之间的边界条件313
4.3 接触热阻边界条件313
4.5 其他边界条件313
5.3 固相率和温度的关系314
5.4 潜热放出的实际处理方法314
6 温度场数值模拟系统流程316
第10章 流动场分析317
1 数学模型317
2 数学模型的离散化317
2.1 离散格式的选择317
2.2 动量方程(Navier-Stoks方程)的离散318
2.3 连续性方程的离散319
3 SOLA-VOF计算方法320
2.4 体积函数的求值320
4 初始条件321
5 边界条件321
5.1 自由表面速度边界条件321
5.2 自由表面压力边界条件322
5.3 型壁速度边界条件322
6 数值稳定性条件323
7 流动与传热藕合计算323
7.1 前言323
7.2 数学模型与数值求解323
8 流动场模拟软件流程325
1 充模过程的数学描述326
1.1 充模过程的基本方程326
第11章 塑料注射成形过程模拟326
1.2 基本方程的简化327
1.3 数学模型及边界条件327
1.4 塑料熔体的黏度模型329
2 一维流动分析329
3 二维流动分析330
4 三维流动分析331
4.1 压力场有限元方程332
4.2 熔体流动前沿位置的确定333
4.3 温度场计算333
4.4 数值计算过程335
5 保压过程分析335
6.1 一维冷却分析338
6 冷却过程分析338
6.2 二维冷却分析340
6.3 三维冷却分析342
第12章 材料成形过程模拟商业软件简介345
1 塑性成形模拟软件345
1.1 体积成形模拟软件345
1.2 冲压成形模拟软件347
2 铸造成形模拟软件349
3 塑料注射成形模拟软件353
3.1 充模流动模拟软件353
3.2 冷却模拟软件356
参考文献357
第3篇 金属塑性成形过程优化设计方法363
第1章 绪论363
1 金属塑性成形理论分析方法概述363
2 基于数值模拟技术的预成形设计方法364
3.1 基于灵敏度分析的正向模拟优化法365
3.2 直接微分法365
3 基于灵敏度分析的模具优化设计方法365
3.3 拟合优化法366
3.4 微观遗传算法366
4 金属塑性成形过程的其他优化设计方法366
4.1 一致变换方法及理论流动模型366
4.2 神经网络形状内插值法367
4.3 改进的约束变尺度法367
2 工程优化设计的数学模型368
2.2 目标函数368
2.1 设计变量368
1 引言368
第2章 工程优化设计方法368
2.3 约束条件369
3 无约束优化方法369
3.1 一维搜索方法370
3.2 梯度法371
3.3 牛顿法372
3.4 变尺度法373
4 约束优化方法373
4.1 Liagrange乘子法374
4.2 外部惩罚函数法(外点法)375
4.3 内部惩罚函数法(内点法)377
5.1 主要目标法378
5.2 加权函数法378
5 多目标优化问题的解法378
第3章 基于有限元模拟技术的反向模拟式设计379
1 引言379
2 有限元反向模拟技术的原理379
3 反向模拟关键应用技术381
3.1 反向模拟与预成形设计的步骤381
3.2 加工硬化现象的处理382
3.3 预锻模模腔形状设计382
3.4 预锻件形状的选择及工序数目的确定382
3.5 反向模拟过程中动态边界条件的确定382
3.6 有限元反向模拟系统的构造383
4 缩口过程的反向模拟及预成形设计385
4.1 室温缩口过程的预成形设计385
4.2 热缩口成形过程的预成形设计386
5 反向模具接触跟踪方法388
5.1 边界条件的确定388
5.2 工序数目的确定389
5.3 通过透平圆盘锻造过程的预成形设计389
6 基于锻件形状复杂程度的控制准则393
6.1 工件形状复杂系数及边界条件控制准则394
6.2 预成形设计应用举例394
第4章 刚(粘)塑性有限元灵敏度分析与模具优化设计方法399
1 引言399
2 刚(粘)塑性有限元基本方程399
3 目标函数与设计变量400
4 灵敏度分析401
4.1 节点速度灵敏度402
4.2 ?的确定402
5 速度灵敏度边界条件403
6 模具优化设计方法的应用技术405
6.1 模具优化设计步骤405
6.2 体积损失的调整407
6.3 有限元网络再划分409
6.4 提高程序运算速度的方法410
7 少无鼓形圆柱体镦粗过程的优化设计410
8 有型腔模具的锻造过程优化设计412
8.1 H形截面轴对称锻件锻造过程(型腔高径比h/b=1)412
8.2 H形截面轴对称锻件锻造过程(型腔高径比h/b=2)412
8.3 齿轮坯锻造过程的优化设计415
9 锻件毛坯形状优化设计方法416
9.1 目标函数417
9.2 优化设计实例419
10 锻件变形均匀性优化控制422
10.1 目标函数422
10.2 灵敏度分析422
10.3 应用实例424
第5章 金属塑性成形过程的微观组织优化425
1 引言425
2 微观组织演变模型425
2.1 动态再结晶425
2.2 静态再结晶426
2.3 晶粒生长426
3 金属塑性成形过程微观组织模拟与优化基本算法426
3.1 遗传算法426
3.2 灵敏度分析方法428
4.1 H形锻件成形过程组织模拟与优化429
4 微观组织模拟与优化实例429
4.2 热挤压成形过程的微观组织模拟与优化430
4.3 基于灵敏度分析方法的微观组织模拟与优化433
第6章 稳态金属成形过程优化设计439
1 稳态成形过程优化设计问题439
2 设计灵敏度分析440
3 二维挤压模具形状优化设计441
4 三维挤压模具形状优化设计443
4.1 设计模型443
4.2 优化实例444
参考文献449
1 基本概念457
1.1 计算机辅助制造的定义457
第4篇 模具计算机辅助制造457
第1章 概论457
1.2 CAM在模具行业的应用现状458
1.3 CAM技术的优势459
2 建立CAM系统的基本过程459
2.1 建立CAM软件系统的过程459
2.2 模具CAM基本功能与内容462
3 发展趋势464
3.1 计算机集成制造系统的重要组成部分-CAM464
3.2 网络化、智能化、最优化465
3.3 虚拟制造技术465
1.2 Ferguson曲线467
1.1 自由曲线的生成与参数方程467
第2章 曲线与曲面467
1 曲线467
1.3 Bezier曲线468
1.4 B样条曲线471
1.5 非均匀有理B样条(NURBS)曲线473
2 曲面474
2.1 概述474
2.2 Coons曲面475
2.3 Bezier曲面475
2.4 B样条曲面476
2.5 NURBS曲面476
2.6 曲面的反求、拼接和互化476
1.1 基本计算机硬件介绍478
第3章 模具CAM的基本组成478
1 硬件系统的组成478
1.2 硬件系统选择的基本原则480
2 软件组成481
2.1 软件系统的分类481
2.2 系统软件481
2.3 CAM应用软件484
第4章 数控编程技术487
1 概述487
1.1 数控加工的基本概念487
1.2 数控机床的组成、分类及发展489
2 编程技术492
2.1 数控加工程序的编制492
2.2 自动编程语言494
2.3 数控自动编程技术的发展496
2.4 校核与真实感仿真技术497
第5章 应用实例与实用软件介绍498
1 冲裁模CAM示例498
1.1 生成钼丝运动轨迹498
1.2 穿丝孔和起割点的自动选取498
1.3 自动编程过程499
2 注塑模具CAM示例500
2.1 2轴加工500
2.2 3轴加工500
3 Mastercam介绍502
3.1 系统特性概述502
3.2 系统的运行环境和流程503
3.3 系统界面及功能504
3.4 用Mastercam编制NC加工程序的实例505
参考文献507
第5篇 快速成形与快速制模511
第1章 概论511
1 引言511
2 快速成形技术发展历史的回顾511
3 快速成形技术的发展511
3.1 光固化成形511
3.2 纸叠层成形512
3.3 选择性激光烧结成形513
3.4 熔丝沉积成形513
3.5 其他方法成形513
4 快速制模、快速制造技术的发展514
3.6 RP软件514
5 快速成形技术的应用515
6 快速成形技术的展望517
第2章 光固化成形518
1 光固化成形原理518
2 光固化成形系统519
3 光固化成形的过程520
4 光固化性树脂521
4.1 光固化性树脂的成分521
4.2 光固化反应522
5 光固化的特性525
5.1 固化形状525
4.3 光固化性树脂应满足的条件525
5.2 固化曲线526
5.3 感光度527
第3章 纸叠层成形529
1 纸叠层成形技术概述529
2 原型件的设计与制造530
2.1 原型件的设计530
2.2 原型件的制造530
3 成形件后处理531
3.1 剥离531
3.2 修补、打磨和抛光531
3.3 表面涂覆531
4 LOM技术应用案例531
4.2 大尺寸、薄壁零件的剖分成形532
4.1 制作大尺寸、薄壁零件存在的问题532
4.3 实现大尺寸、薄壁零件制造的软件533
第4章 选择性激光烧结成形535
1 选择性激光烧结成形原理535
2 成形系统及软件535
2.1 控制系统535
2.2 主机536
2.3 SLS成形的软件537
2.4 商品化的SLS成形设备539
3 烧结成形机理540
3.1 粉末特性540
3.2 粉末热性能的模型541
3.3 粉末烧结的基本理论542
3.4 含有高分子粘结剂的混合物烧结性能548
4 SLS成形工艺549
4.1 基本的工艺方法和工艺过程550
4.2 工艺方案的确定和参数的选择553
4.3 烧结收缩及其影响因素555
4.4 成形件的力学性能及其影响因素558
4.5 金属粉末的SLS成形559
4.6 金属陶瓷和陶瓷的SLS成形560
5 激光烧结技术的应用561
5.1 基于SLS技术的间接制模技术561
5.2 转换法制造金属模具561
5.3 激光烧结工艺在快速开发新产品和快速制模应用中的优点563
5.4 SLS方法的其他应用563
1.1 工艺路线566
1 软模技术566
第5章 快速制模技术566
1.2 原型件的准备567
1.3 制作硅橡胶模具567
1.4 浇注品的制作567
2 过渡模技术570
3 硬模技术570
3.1 直接加工金属模具571
3.2 用SLS烧结铸型571
3.3 基于快速原型的喷涂法571
3.4 陶瓷壳砂型法571
3.5 石墨研磨法571
4 金属薄板成形模具的快速制造572
4.1 采用填充法制造金属板料拉深模572
4.2 采用芯体表层浇铸法的制模技术577
参考文献579
第6篇 模具材料及热处理583
第1章 概论583
1 模具材料的类别583
2 模具材料的性能589
2.1 模具钢的主要使用性能589
2.2 模具钢的主要工艺性能589
3 模具材料的热处理590
4 模具材料的选用595
4.1 冷作模具的选用595
4.2 热作模具材料的选用596
4.3 塑料模具的选用598
1 对冷作模具钢的要求600
第2章 冷作模具钢600
2 碳素工具钢601
2.1 碳素工具钢的热处理工艺与性能601
2.2 T10(A)钢的热处理工艺与性能604
3 低合金工模具钢611
3.1 Gr2(Gr15)钢613
3.2 CrWMn钢621
3.3 9Mn2V钢624
3.4 9SiCr钢629
3.5 6CrW2Si钢632
3.6 60Si2Mn钢634
3.7 GD钢635
3.8 常用低合金工具钢的性能比较638
4 微变形模具钢639
4.1 中铬微变形模具钢的热处理工艺与性能640
4.2 高铬微变形模具钢的热处理工艺与性能645
5 高速钢657
5.1 高速钢常规热处理工艺与性能657
5.2 高速钢冷作模具热处理工艺与性能659
5.3 高速钢的等温淬火工艺与性能665
6 基体钢666
6.1 基体钢的常规热处理工艺667
6.2 65Nb(65Cr4W3Mo2VNb)钢672
6.3 012A1(5Cr4Mo3SiMnVA1)钢677
6.4 CG2(6Cr4Mo3Ni2WV)钢681
6.5 LM1钢与LM2钢685
7.1 LD钢689
7 高强韧高耐磨钢689
7.2 GM钢692
7.3 ER5钢696
8 火焰淬火模具钢699
第3章 热作模具钢702
1 热作模具钢的分类702
2 热作模具钢的化学成分702
3 热作模具钢的使用性能703
4 低合金热作模具钢703
4.1 5CrNiMo钢704
4.2 5CrMnMo钢705
4.3 4CrMnSiMoV钢705
4.4 3Cr2MoWVNi钢706
4.5 5Cr2NiMoVSi与45Cr2NiMoVSi钢707
4.6 7Cr3与8Cr3钢708
5 中合金热作模具钢709
5.1 3Cr2W8V钢709
5.2 5Cr4W5Mo2V钢711
5.3 5Cr4Mo3SiMnVAl(012A1)钢713
5.4 4Cr5MoSiV(H11)钢714
5.5 4Cr5MoSiV1(H13)钢716
5.6 3Cr3Mo3W2V(HM-1)钢719
5.7 4Cr3Mo3SiV(H10)钢720
5.8 4Cr5W2VSi钢721
5.9 4Cr3Mo2NiVNbB(HD)钢723
6 高合金热作模具钢(70Mn15)725
7.1 4Cr14Ni14Mo2W钢726
7 奥氏体耐热钢726
8 高温抗蚀模具钢727
7.2 AH与5Mn15钢727
第4章 塑料模具钢730
1 塑料模具钢的性能730
1.1 塑料模具的分类及工作条件730
1.2 塑料模具的主要失效形式730
1.3 塑料模具对材料的性能要求731
2 塑料模具常用材料742
2.1 塑料模具材料的选择原则742
2.2 常用的塑料模具材料分类745
3 塑料模具的热处理748
3.1 塑料模具热处理的常用设备748
3.3 塑料模具的热处理方法及规范750
3.2 塑料模具热处理的基本技术要求750
第5章 特殊模具钢775
1 无磁模具钢775
1.1 热处理工艺775
1.2 热处理工艺对性能的影响776
2 铸造模具钢777
3 粉末冶金模具钢779
第6章 其他模具材料784
1 铸铁784
2 硬质合金和钢结硬质合金787
2.1 硬质合金787
2.2 钢结硬质合金791
3 有色金属及其合金796
3.1 低熔点合金797
3.2 锌基合金800
3.3 铜合金803
第7章 冷作模具材料的选用805
1 冷作模具材料的性能比较805
2 常用冷作模具材料的选用806
第8章 热作模具材料的选用817
1 常用热作模具材料的性能比较817
2.2 热挤压模具材料的选用821
2.3 压铸模具材料的选用821
2.4 高速锤锻模具用钢的选用821
2.1 锻模材料的选用821
2 常用热作模具材料的选用821
第9章 模具钢渗碳和碳氮共渗838
1 模具表面强化处理概述838
2 模具钢渗碳840
2.1 模具钢渗碳的目的840
2.2 渗碳工艺的主要特点841
2.3 渗碳的主要技术要求841
2.4 渗碳钢的原始含碳量对渗层的影响842
2.5 渗碳钢中的合金元素对渗层形成的影响842
2.6 合金元素对渗碳钢工艺性能的影响843
2.7 渗碳的主要工艺参数843
2.8 渗碳工艺844
3 模具钢的碳氮共渗850
4.1 低碳高合金钢渗层854
4 模具钢渗碳和碳氮共渗层组织与性能854
4.2 高碳低合金钢渗层855
4.3 中高碳高合金钢渗层856
4.4 含硅高合金钢渗层858
5 模具钢渗碳后的热处理858
6 模具钢渗碳热处理的缺陷860
第10章 模具钢的渗氮及氮碳共渗863
1 模具钢的渗氮863
1.1 渗氮工艺863
1.2 气体渗氮865
1.3 液体渗氮867
1.4 渗氮新工艺868
2 氮碳共渗870
2.1 气体氮碳共渗871
2.2 液体氮碳共渗874
3 渗层形成机理875
3.1 Fe-N状态图875
3.2 渗氮层的形成机理876
3.3 氮碳共渗的渗层组织879
4 渗氮和氮碳共渗的渗层组织性能的检测881
4.1 渗层深度的显示和测量881
4.2 渗氮和氮碳共渗金相组织检查881
4.3 渗层脆性的检查882
5 渗氮和氮碳共渗的缺陷及其预防措施882
第11章 模具钢渗硼885
1 渗硼工艺885
1.1 固体粉末渗硼法886
1.2 电解渗硼888
1.3 盐浴渗硼法889
1.4 气体渗硼890
2 渗硼层形成机理890
2.1 渗硼组织形成机理890
2.2 硼扩散层894
2.3 合金元素的作用895
2.4 硼针的择优取向896
3 渗硼层的检查897
3.1 组织显示897
3.2 渗硼层形态897
3.3 硼化物层深度测量898
3.5 硼化物脆性及测量方法899
3.4 硼化物硬度测量899
4 渗硼组织900
4.1 渗硼前后热处理900
4.2 渗层组织900
5 渗硼层缺陷902
第12章 模具钢渗铬904
1 渗铬工艺904
1.1 概述904
1.2 固体渗铬905
1.3 气体渗铬907
1.4 液体渗铬907
2 渗铬层的形成机理908
3.1 T10钢的渗铬层组织和性能911
3 渗铬层的组织911
3.2 Cr12MoV钢的渗铬层组织913
4 渗铬层性能913
5 稀土-铬共渗和碳铬共渗工艺915
5.1 稀土-铬共渗915
5.2 碳铬共渗917
6 渗铬层缺陷918
第13章 其他表面强化方法923
1 碳化钛涂层923
1.1 碳化钛气相涂层923
1.2 碳化钛液体涂层925
1.3 碳化钛固体涂层925
2.2 电镀、刷镀与电铸926
2.1 激光强化技术926
2 其他强化方法926
2.3 热喷涂927
2.4 喷丸强化928
2.5 电火花强化928
参考文献928
第7篇 模具设计通用基础标准933
第1章 技术制图933
1 基本规定933
1.1 图框格式和图幅尺寸933
1.2 标题栏和明细栏934
1.3 比例934
1.4 图线934
1.5 剖面符号934
2.1 投影法936
2 图样画法936
2.2 视图937
2.3 剖视图和断面图937
3 注法943
3.1 尺寸注法943
3.2 尺寸公差与配合注法944
3.3 圆锥的尺寸和公差注法944
3.4 简化注法949
4 常用结构要素和常用件的表示法952
4.1 螺纹及螺纹紧固件表示法952
4.2 弹簧画法954
4.3 中心孔表示法954
1.1 术语及定义957
1 尺寸极限(公差)与配合957
第2章 极限与配合957
1.2 公差、偏差和配合的基本规定960
1.3 标准公差和基本偏差966
1.4 孔、轴的极限偏差966
1.5 公差带和配合的选择1014
1.6 配制配合1016
2 未注公差的线性和角度尺寸的一般公差1023
2.1 一般公差的公差等级和极限偏差1023
2.2 适用的尺寸和图样表示法1024
3 统计尺寸公差1025
3.1 统计尺寸公差的含义1025
3.2 规定实际尺寸概率分布特性的方案及标注1025
3.3 统计尺寸公差在孔、轴配合中的应用1026
1.1 术语及定义1034
第3章 形状和位置公差1034
1 术语、定义和符号1034
1.2 形位公差的符号1036
1.3 形位公差带的定义1037
2 形位公差数值及应用1044
3 公差原则及应用1052
3.1 独立原则的应用1053
3.2 包容要求的应用1055
3.3 最大实体要求的应用1056
3.4 最小实体要求的应用1059
4 形位公差在图样上的标注方法1061
1 术语、定义、符号和代号1066
1.1 表面粗糙度术语及定义1066
第4章 表面粗糙度1066
1.2 表面粗糙度常用符号与代号1070
2 表面粗糙度参数及其数值1071
2.1 评定表面粗糙度的参数及其数值系列1071
2.2 取样长度的数值和选用1072
3 表面粗糙度参数值的选择1072
4 表面粗糙度在图样上的标注方法1075
第5章 量和单位1077
1 国际单位制与法定计量单位1077
1.1 国际单位制1077
1.2 法定计量单位1077
1.3 法定计量单位的使用方法1079
2 常见非法定计量单位的换算1081
参考文献1085
热门推荐
- 1973178.html
- 3564678.html
- 107280.html
- 1133772.html
- 2791192.html
- 55589.html
- 1965749.html
- 3671128.html
- 465692.html
- 3276374.html
- http://www.ickdjs.cc/book_2482304.html
- http://www.ickdjs.cc/book_1754762.html
- http://www.ickdjs.cc/book_558012.html
- http://www.ickdjs.cc/book_2814338.html
- http://www.ickdjs.cc/book_3554482.html
- http://www.ickdjs.cc/book_657688.html
- http://www.ickdjs.cc/book_1689593.html
- http://www.ickdjs.cc/book_1136130.html
- http://www.ickdjs.cc/book_3550633.html
- http://www.ickdjs.cc/book_3633416.html