图书介绍
数字化加工过程质量控制方法与技术【2025|PDF|Epub|mobi|kindle电子书版本百度云盘下载】
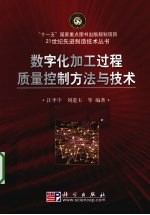
- 江平宇,刘道玉等编著 著
- 出版社: 北京:科学出版社
- ISBN:9787030280138
- 出版时间:2010
- 标注页数:282页
- 文件大小:46MB
- 文件页数:297页
- 主题词:数控机床-加工-质量控制
PDF下载
下载说明
数字化加工过程质量控制方法与技术PDF格式电子书版下载
下载的文件为RAR压缩包。需要使用解压软件进行解压得到PDF格式图书。建议使用BT下载工具Free Download Manager进行下载,简称FDM(免费,没有广告,支持多平台)。本站资源全部打包为BT种子。所以需要使用专业的BT下载软件进行下载。如BitComet qBittorrent uTorrent等BT下载工具。迅雷目前由于本站不是热门资源。不推荐使用!后期资源热门了。安装了迅雷也可以迅雷进行下载!
(文件页数 要大于 标注页数,上中下等多册电子书除外)
注意:本站所有压缩包均有解压码: 点击下载压缩包解压工具
图书目录
《21世纪先进制造技术丛书》序1
前言1
第1章 绪论1
1.1 数字化加工过程质量控制概述1
1.1.1 数字化加工多源多工序过程质量控制的提出1
1.1.2 数字化加工多源多工序过程质量控制的特征与内涵2
1.2 数字化加工过程闭环质量控制3
1.2.1 数字化加工过程的稳态生产要求3
1.2.2 数字化加工过程质量控制的闭环流程4
1.3 数字化加工过程质量控制稳态的实现模式5
1.3.1 多源多工序过程质量控制体系结构5
1.3.2 多源多工序过程质量控制实现框架与执行逻辑7
1.4 实现多源多工序过程质量控制的关键技术11
1.4.1 数字化加工的工序流配置技术11
1.4.2 面向工序流的数字检测传感网络11
1.4.3 工序流误差传递建模与关键工序结点识别技术12
1.4.4 工序结点质量稳态控制技术12
1.4.5 工序流质量实时跟踪技术13
1.4.6 工序流质量变化管理技术13
1.4.7 加工质量缺陷诊断与设备健康维护技术13
第2章 数字化加工的工序流配置14
2.1 多工艺路线规划14
2.1.1 数字化加工的多工序流规划策略14
2.1.2 多工艺路线规划数学模型16
2.1.3 基于蚁群算法的多工艺路线求解18
2.1.4 基于蚁群算法的非线性多工艺路线规划实例21
2.2 工序公差的优化分配24
2.2.1 多工序多特征公差优化思路24
2.2.2 特征成本函数构建25
2.2.3 基于ATC的工序公差优化求解27
2.3 工序流配置建模与优化32
2.3.1 面向多工序流的零件聚类分析思路32
2.3.2 基于加权有向图的零件工艺描述模型33
2.3.3 基于群体智能算法的工序流优化37
2.3.4 实例分析41
2.4 本章小结45
第3章 数字化测量与传感网络46
3.1 数字化加工过程多源质量数据的获取方法46
3.1.1 数字化加工过程闭环质量控制的数据需求特点46
3.1.2 数字化检测传感网络的提出47
3.2 数字检测仪器的配置48
3.2.1 基于零件加工特征的检测仪器配置框架48
3.2.2 零件加工特征网络分析49
3.2.3 检测仪器配置空间建模56
3.2.4 基于本体的检测仪器配置57
3.3 工序物流信息的RFID读写器配置67
3.3.1 RFID数据采集网络设计67
3.3.2 RFID数据获取预处理70
3.4 数字检测传感网络性能评价73
3.4.1 数字检测传感网络模型73
3.4.2 基于复杂网络理论的数字检测传感网络性能分析76
3.5 工序尺寸数据在线测量技术79
3.5.1 数控加工轴外径在线测量系统组成79
3.5.2 测量系统设计与试验平台搭建80
3.5.3 测量系统误差评定85
3.6 叶片类复杂曲面零件的测量仪研制及其加工误差评定90
3.6.1 基于Keyence激光传感器的数控测量仪90
3.6.2 测量仪误差测定与补偿91
3.6.3 叶片类复杂零件的测量路径规划96
3.6.4 叶片型线数字化建模103
3.6.5 叶片型线理论曲线与测量曲线的误差比对分析107
3.6.6 叶片型线加工误差评估109
3.7 本章小结112
第4章 工序误差传递建模与解算113
4.1 多源多工序误差传递网络基本概念113
4.1.1 误差传递网络的提出113
4.1.2 误差传递网络构建思想114
4.2 误差传递网络建模115
4.2.1 误差传递网络建模原理115
4.2.2 误差传递网络建模步骤117
4.2.3 误差传递网络生成119
4.3 误差传递网络特性量测120
4.3.1 网络基本特性定义120
4.3.2 网络传递效应量测121
4.4 误差传递网络实证分析123
4.4.1 发射架箱体零件加工误差传递网络构建123
4.4.2 小世界效应验证124
4.4.3 网络特性分析126
4.5 基于误差传递网络的工序流波动效应评价131
4.5.1 工序流波动分析的基本原理131
4.5.2 波动传递模型与波动传递网络构建132
4.5.3 波动源评价与辨识135
4.5.4 实例分析136
4.6 本章小结139
第5章 数字化加工的质量稳态控制140
5.1 数字化加工过程质量稳态控制概述140
5.1.1 基于(近)零缺陷的稳态生产过程140
5.1.2 零缺陷稳态生产过程的实现方法140
5.2 多种生产模式下的工序质量控制方法141
5.2.1 大批量生产模式的工序质量控制图141
5.2.2 大规模定制生产模式下的工序质量控制图146
5.2.3 小批量生产模式下的工序质量控制图148
5.3 基于神经网络-数值拟合的控制图模式识别153
5.3.1 工序控制图的基本模式153
5.3.2 控制图模式识别的神经网络-数值拟合模型155
5.3.3 控制图模式识别过程训练与仿真157
5.4 基于小波理论的工序质量监控与诊断集成160
5.4.1 工序质量监控与诊断集成框架160
5.4.2 基于小波多尺度理论的工序质量监控161
5.4.3 基于信号融合的工序质量诊断164
5.5 工序流过程能力评价166
5.5.1 工序流波动轨迹图166
5.5.2 基于合格率的多工序能力指数模型169
5.5.3 实例分析172
5.6 本章小结175
第6章 基于设备e-QC模型的工件加工质量跟踪177
6.1 基于设备e-QC模型的工件加工质量跟踪概述177
6.1.1 加工过程质量信息的实时性需求分析177
6.1.2 基于设备e-QC模型的加工过程质量信息跟踪逻辑实现架构177
6.2 面向加工设备的e-QC结点模型178
6.2.1 e-QC结点模型的图式概念描述178
6.2.2 e-QC结点模型的组成要素界定180
6.2.3 e-QC结点的参考实现框架180
6.2.4 实例分析183
6.3 工件质量信息共享控制方法185
6.3.1 质量信息共享基本概念185
6.3.2 质量信息共享控制数学描述187
6.3.3 质量信息共享控制实现算法188
6.4 基于TIT网络的工件质量信息跟踪的实现189
6.4.1 模板及模板结构树189
6.4.2 模板实例的动态更新190
6.4.3 基于TIT网络的工序质量信息跟踪实现算法194
6.4.4 实例分析196
6.5 本章小结199
第7章 数字化加工的工件质量变化管理200
7.1 工件质量变化管理理念及其实现框架200
7.1.1 工件质量变化管理相关概念200
7.1.2 工件质量变化管理体系结构201
7.2 基于Blog平台的工件质量控制知识管理202
7.2.1 基于Blog平台的工件质量控制知识管理系统架构202
7.2.2 基于情境的质量控制知识模型204
7.2.3 基于情境的质量控制知识本体建模208
7.2.4 基于情境的质量知识检索与推送211
7.3 工件加工误差的可视化评估与综合分析216
7.3.1 基于质量控制工具集成的工件加工误差可视化评估216
7.3.2 工件关联工序质量特性变化的回归分析218
7.4 基于加权误差传递网络的工件质量变化预测224
7.4.1 加权误差传递网络建模原理224
7.4.2 加权误差传递网络的形成224
7.4.3 工件质量变化预测225
7.5 本章小结228
第8章 数字化加工的误差溯源229
8.1 数字化机械加工误差溯源概述229
8.1.1 数字化机械加工误差及其误差源分类229
8.1.2 数字化机械加工误差溯源基本原理233
8.2 数字化机械加工过程质量智能诊断领域本体建模233
8.2.1 数字化机械加工过程智能诊断模型233
8.2.2 数字化机械加工过程质量诊断领域本体的层次结构235
8.2.3 领域本体建立与层次结构实现238
8.3 基于粗糙集的质量诊断知识库建立241
8.3.1 诊断知识的分类与获取241
8.3.2 基于粗糙集的控制图异常诊断规则提取242
8.3.3 诊断规则知识的形成245
8.4 数字化机械加工过程质量异常智能诊断决策246
8.4.1 质量异常诊断决策原理246
8.4.2 质量异常诊断决策实现247
8.4.3 实例分析248
8.5 基于支持向量机的工序质量异常诊断250
8.5.1 数字化切削加工过程的监控状态量250
8.5.2 数字化切削加工过程状态信号特征提取250
8.5.3 支持向量机的异常状态编码与诊断过程实现252
8.6 本章小结255
第9章 数字化加工的设备健康维护257
9.1 基于Logistic回归的设备综合故障概率指标257
9.1.1 设备服役性能分析与维护原理257
9.1.2 Logistic回归模型258
9.1.3 设备综合故障概率指标定义及计算259
9.2 数控设备服役性能分析与预测260
9.2.1 基于SVR的设备服役寿命预测260
9.2.2 基于蒙特卡罗仿真试验与结果分析261
9.3 设备群性能退化与维护建模265
9.3.1 设备退化模型的建立265
9.3.2 基于视情维护的多装备联合决策模型267
9.4 基于蒙特卡罗仿真的维护决策过程求解270
9.4.1 设备退化与维护过程模拟271
9.4.2 设备状态检查过程271
9.4.3 备件库存量模型272
9.4.4 期望费用的计算272
9.4.5 实例分析273
9.5 本章小结275
参考文献277
热门推荐
- 3136019.html
- 1307913.html
- 549052.html
- 325649.html
- 1802696.html
- 919216.html
- 1258702.html
- 2438924.html
- 1373893.html
- 61866.html
- http://www.ickdjs.cc/book_3603713.html
- http://www.ickdjs.cc/book_533710.html
- http://www.ickdjs.cc/book_3172770.html
- http://www.ickdjs.cc/book_2462217.html
- http://www.ickdjs.cc/book_894872.html
- http://www.ickdjs.cc/book_616881.html
- http://www.ickdjs.cc/book_838205.html
- http://www.ickdjs.cc/book_2313925.html
- http://www.ickdjs.cc/book_2194478.html
- http://www.ickdjs.cc/book_1626838.html