图书介绍
实用车工技术手册【2025|PDF|Epub|mobi|kindle电子书版本百度云盘下载】
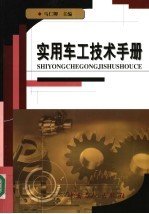
- 马仁卿主编 著
- 出版社: 北京:中国石化出版社
- ISBN:7801646258
- 出版时间:2004
- 标注页数:526页
- 文件大小:26MB
- 文件页数:544页
- 主题词:车削-技术手册
PDF下载
下载说明
实用车工技术手册PDF格式电子书版下载
下载的文件为RAR压缩包。需要使用解压软件进行解压得到PDF格式图书。建议使用BT下载工具Free Download Manager进行下载,简称FDM(免费,没有广告,支持多平台)。本站资源全部打包为BT种子。所以需要使用专业的BT下载软件进行下载。如BitComet qBittorrent uTorrent等BT下载工具。迅雷目前由于本站不是热门资源。不推荐使用!后期资源热门了。安装了迅雷也可以迅雷进行下载!
(文件页数 要大于 标注页数,上中下等多册电子书除外)
注意:本站所有压缩包均有解压码: 点击下载压缩包解压工具
图书目录
第1章 车削加工常用资料1
1.1 常用字母、罗马数字与国家部分标准代号1
1.1.1 常用字母表与罗马数字表1
目录1
1.1.2 常用有关的符号3
1.1.3 国家部分标准代号12
1.2 法定计量单位与常见非法定计量单位12
1.2.1 中华人民共和国法定计量单位12
1.2.2 法定计量单位与常见非法定计量单位换算14
1.2.3 法定计量单位常用符号的错误写法18
1.2.4 平面角的角、分、秒与弧度换算20
1.3 车削加工常用零件结构要素标准21
1.3.1 锥度与锥角系列21
1.3.2 中心孔类型与结构尺寸22
1.3.4 滚花24
1.3.3 球面半径24
1.3.5 零件倒圆与倒角25
1.3.6 回转面与端面砂轮越程槽26
1.4 常用材料的有关数据27
1.4.1 常用金属材料的熔点、热导率与比热容27
1.4.2 常用材料的线胀系数28
1.4.3 常用材料的密度28
1.4.4 常用金属材料的弹性模量和弹性剪切模量29
1.4.5 常用材料滑动和滚动摩擦系数的概值29
1.5 热处理及表面处理常识30
1.5.1 热处理常识30
1.5.2 化学热处理常识32
1.5.3 表面处理常识32
1.6.1 直齿圆柱齿轮渐开线齿形的近似画法34
1.6 直齿圆柱齿轮渐开线齿形的近似画法及冷缠弹簧心轴直径的计算34
1.6.2 冷缠拉力弹簧心轴直径的计算与压力弹簧数据表35
1.7 基本机械传动计算及平带、V带与直齿圆柱齿轮传动计算37
1.7.1 普通平带传动计算37
1.7.2 普通V带传动计算39
1.7.3 直齿圆柱齿轮传动计算42
1.8 圆柱蜗杆传动精度与公差53
1.8.1 圆柱蜗杆传动精度等级与其公差53
1.8.2 蜗杆传动的侧隙规定57
1.8.3 蜗杆蜗轮图样标注与其齿坯的尺寸形状公差58
第2章 技术测量及公差与配合62
2.1 技术测量的基本概念及量具与测量方法的分类62
2.1.1 技术测量的基本概念62
2.1.2 计量器具与测量方法的分类62
2.2.1 计量器具的度量指标63
2.2 计量器具的度量指标及常用量具量仪63
2.2.2 常用量具与量仪简介64
2.2.3 量块与其附件应用简介70
2.2.4 常用量具与量仪正确操作姿势的示范71
2.3 测量误差的分析及随机误差的特性与处理74
2.3.1 测量误差的来源74
2.3.2 测量误差的分类74
2.3.3 随机误差的特性与处理75
2.4 计量器具的选择方法及其主要根据76
2.4.1 测量不确定度和验收极限76
2.4.2 计量器具的选择方法77
2.5 量具、量仪测量的极限误差及其允许误差79
2.5.1 常用量具、量仪测量的极限误差79
2.5.2 常用测微量具、量仪测量的允许误差80
2.6 《公差与配合》新国标的基本结构及公差与配合的基准制81
2.6.1 标准公差系列81
2.5.3 量块测量的允许误差81
2.6.2 基本偏差系列82
2.6.3 公差与配合的基准制82
2.6.4 公差带代号、配合代号与其表示方法82
2.7 标准公差及公差带极限偏差84
2.7.1 标准公差数值表84
2.7.2 新国标公差等级与旧国标精度等级对照84
2.7.3 孔、轴的公差带极限偏差表85
2.7.4 未注公差的线性和角度尺寸的极限偏差91
2.8 圆锥角公差及未注公差角度的极限偏差92
2.8.1 圆锥角的公差数值表92
2.8.2 圆锥直径公差所能限制的最大圆锥角误差93
2.9.1 形状和位置公差的定义、符号与图样标注法94
2.8.3 未注公差角度的极限偏差94
2.9 形状及位置公差94
2.9.2 形位公差带的定义、标注和解释97
2.9.3 图样上注出的形位公差值和未注形位公差值104
2.9.4 形位公差原则106
2.9.5 形位误差检测规定107
2.9.6 形位误差常用检测方案109
2.10 表面粗糙度评定参数与图样标注及其检测方法118
2.10.1 表面粗糙度评定参数与其数值118
2.10.2 表面粗糙度符号、代号与其标注方法119
2.10.3 表面粗糙度的检测方法123
2.10.4 新国标的粗糙度与旧国标的光洁度对照表123
2.10.5 表面粗糙度评定参数值Ra与加工方法的选择124
3.1.1 产品名称、用途、特性和工艺方法表示符号127
第3章 金属材料切削加工性能的分析及金属切削的基本规律127
3.1 产品名称、用途、特性和工艺方法表示符号及牌号表示方法127
3.1.2 钢号表示方法128
3.1.3 金属材料力学性能指标的名词解释129
3.1.4 黑色金属硬度与强度换算值130
3.2 铸铁及碳素铸钢件牌号表示方法135
3.2.1 铸铁牌号、化学成分、力学性能与用途135
3.2.2 铸钢牌号表示方法137
3.2.3 钢的分类138
3.3 钢材的涂色标记及常用钢的火花鉴别法140
3.3.1 钢材的涂色标记140
3.3.2 常用钢的火花鉴别法140
3.4 常用钢的牌号、化学成分及其力学性能142
3.4.1 碳素结构钢牌号、化学成分和力学性能142
3.4.2 优质碳素钢的牌号、化学成分和力学性能144
3.4.3 合金结构钢的统一数字代号、牌号、化学成分和力学性能145
3.4.4 常用弹簧钢与不锈钢的牌号、化学成分和力学性能146
3.4.5 常用碳素工具钢与合金工具钢的牌号、化学成分和试样淬火硬度147
3.5 非铁金属及合金产品牌号表示方法与分类148
3.5.1 常用非铁金属与其合金产品牌号表示方法148
3.5.2 常用非铁金属与其合金的分类151
3.5.3 铸造铝合金的牌号、代号、主要元素、杂质限量、铸造方法、合金状态、力学性能与热处理规范152
3.5.4 铸造铝合金牌号表示方法、主要化学元素和含量与牌号示例157
3.5.5 铜与铜合金拉制棒和挤制棒的牌号、状态和力学性能159
3.5.6 铸造铜合金的牌号、名称、主要化学成分、杂质限量、铸造方法、力学性能和主要特性163
3.6 金属材料切削加工性能及相对切削加工性能的分析169
3.6.1 金属材料切削加工性能的概述169
3.6.2 金属材料切削加工性能的主要影响因素169
3.6.4 金属材料切削加工性能的评定指标与方法173
3.6.3 改善金属材料切削加工性能的主要方法173
3.6.5 金属材料相对切削加工性能的简介174
3.7 金属切削过程的变形规律及切屑种类与其形态变化175
3.7.1 车削加工的运动与工件上所出现的表面175
3.7.2 车削过程变形区的划分175
3.7.3 金属切削过程的变形规律176
3.7.4 切屑的种类与其形态的变化177
3.7.5 积屑瘤的形成、作用与其主要影响因素178
3.7.6 金属工件已加工表面的冷作硬化179
3.8 切削力及切削功率179
3.8.1 车削加工的切削力179
3.8.2 影响切削力的主要因素180
3.8.3 切削力的试验测量值与经验公式的建立182
3.8.4 切削力与切削功率计算的举例187
3.8.5 切削力的修正系数与其数值189
3.9 切削热及切削温度192
3.9.1 切削热的来源与传散192
3.9.2 切削温度193
3.9.3 切削温度的主要影响因素193
3.10 刀具的磨损及刀具的耐用度196
3.10.1 刀具磨损的形式196
3.10.2 刀具磨损的原因197
3.10.3 刀具磨损的过程与磨钝标准198
3.10.4 刀具耐用度的定义和切削用量与刀具耐用度之间的关系式200
3.10.5 刀具合理耐用度的制定原则201
4.1.3 我国现用车刀材料的简介204
4.1.1 常用刀具材料基本特性204
4.1.2 常用刀具材料基本特性的优劣顺序204
4.1 刀具材料必须具备的基本特性204
第4章 刀具材料、几何参数及手工刃磨204
4.2 刀具材料合理选择的主要依据及其基本原则209
4.2.1 影响刀具材料合理选择的主要因素209
4.2.2 刀具材料合理选择的主要依据210
4.2.3 刀具材料合理选择的基本原则210
4.3 车刀切削部分的构造要素及静止基准系的切削角度211
4.3.1 车刀切削部分构造要素的名称和定义211
4.3.2 车刀静止基准系与切削角度的定义211
4.4 车刀工作角度的主要影响因素213
4.4.1 进给运动对车刀工作角度的影响214
4.4.2 车刀装夹得高和低对车刀工作角度的影响215
4.4.3 车刀装夹得左右歪斜对车刀工作角度的影响216
4.5 车刀合理几何参数的选择原则216
4.5.1 车刀过渡刃的形式与参数217
4.5.2 车刀的刃口形式与刃口参数218
4.5.3 车刀前刀面的形状与基本类型219
4.5.4 车刀基本切削角度的作用与其选择原则219
4.5.5 车刀合理切削角度的参考值223
4.6 车刀的基本类型及其结构形式224
4.6.1 焊接式和机夹式高速钢车刀的基本类型224
4.6.2 焊接式硬质合金车刀的基本类型227
4.6.3 机夹不重磨式硬质合金车刀的基本类型228
4.6.4 机夹不重磨式硬质合金车刀的简介228
4.7 在车削加工中影响断屑的主要因素及常用断屑的方法233
4.7.1 影响断屑的主要因素233
4.7.2 断屑槽断屑台与断屑块进行断屑的简介235
4.7.3 调节切削用量与改变切削角度进行断屑236
4.8 刀具的手工刃磨及其步骤236
4.8.2 根据刀具材料选用砂轮与手工刃磨刀具的步骤237
4.8.1 手工刃磨刀具的安全守则与注意事项237
4.8.3 砂轮刃磨后的刀具以油石进行手工研磨238
4.8.4 刀具刃磨切削角度的检验239
4.9 先进车刀的介绍240
4.9.1 45°强力切削车刀240
4.9.2 75°机械夹固式高速切削车刀241
4.9.3 90°银白屑车刀241
4.9.4 93°细长轴精车刀242
4.9.5 淬硬钢外圆车刀243
4.9.6 45°机械夹固式奥氏体不锈钢外圆车刀244
4.9.7 球状切屑的螺纹车刀245
4.9.8 山形刃屋脊式下料切断刀245
4.9.9 90°机夹式集屑车刀246
4.9.10 90°脆铜卷屑车刀247
4.10 先进群钻的简介248
4.10.1 基本群钻的几何参数248
4.10.2 钻铸铁群钻的几何参数249
4.10.3 钻不锈钢断屑群钻的几何参数250
4.10.4 钻紫铜群钻的几何参数251
4.10.5 钻黄铜群钻的几何参数252
第5章 卧式车床型号构造、传动系统、精度检验与数控机床简介253
5.1 金属切削机床的型号编制方法253
5.1.1 通用机床型号的表示方法253
5.1.2 最早建厂和生产车床的企业名称与代号256
5.1.3 金属切削机床车床类统一名称与组、系的划分257
5.1.4 已生产在用卧式车床型号的简介259
5.2 卧式车床的构造、性能、基本类型及其技术规格和加工范围260
5.2.1 卧式车床的基本构造260
5.2.3 卧式车床的基本类型261
5.2.2 卧式车床的性能261
5.2.4 常用卧式车床的技术规格262
5.2.5 卧式车床的加工范围264
5.3 卧式车床的传动系统分析及C620-1型车床传动系统的特点264
5.3.1 卧式车床床头变速箱的传动系统分析266
5.3.2 卧式车床进给箱的传动系统分析269
5.3.3 卧式车床溜板箱的传动系统分析270
5.4 卧式车床的维护保养和润滑及其有关的安全技术和安全操作规则272
5.4.1 卧式车床的维护与保养272
5.4.2 卧式车床的润滑273
5.4.3 车工应掌握的安全技术275
5.4.4 卧式车床的安全操作规则277
5.5 卧式车床的精度标准及其精度检验277
5.5.1 卧式车床精度标准的简介277
5.5.2 普通精度级卧式车床几何精度主要检验项目的检验278
5.5.3 精密精度级卧式车床工作精度的检验287
5.5.4 卧式车床的精度对车削加工零件质量的影响288
5.6 影响加工精度的基本因素及其改善措施288
5.6.1 影响加工尺寸精度的基本因素及其改善措施288
5.6.2 影响加工形状精度的基本因素及其改善措施289
5.6.3 影响加工位置精度的基本因素及其改善措施291
5.7 工件加工缺陷的原因及其消除、车床主要部位配合间隙的调整292
5.7.1 工件出现加工缺陷的主要原因及其消除的方法292
5.7.2 卧式车床主要部位配合间隙的调整293
5.8 车削振动的原因及消除措施297
5.8.1 车削振动的主要类型及其特征297
5.8.2 产生自激振动的主要原因及其主要影响因素297
5.8.3 消除自激振动的主要措施299
5.9 提高卧式车床生产率的基本途径301
5.9.1 单件工时的组成301
5.9.2 缩短机动时间提高生产率302
5.9.3 缩短辅助时间提高生产率304
5.9.4 采用先进刀具、创新工艺技术与数控机床提高生产率309
5.10 数控机床的简介及简易数控车床的改装310
5.10.1 数控机床的概述310
5.10.2 数控机床的分类312
5.10.3 数控机床的优点313
5.10.4 数控机床的工作原理313
5.10.5 简易数控车床技术改装的主要环节与具体问题320
第6章 车削加工的经济精度和车削步骤322
6.1 机械加工的精度及其基本概念322
6.1.1 加工的尺寸精度322
6.1.2 加工的形状精度322
6.2.2 加工误差对加工精度的影响323
6.2.1 产生加工误差的主要根源323
6.2 产生加工误差的根源及其对加工精度的影响323
6.1.3 加工的位置精度323
6.2.3 机床调整误差或试切对刀误差对加工尺寸精度的影响327
6.3 提高车削加工尺寸精度的方法及限制加工精度的主要因素327
6.3.1 车削加工提高尺寸精度的方法327
6.3.2 机床调整误差或试切对刀误差对加工尺寸精度的影响328
6.3.3 机床、夹具、刀具的制造误差与磨损对加工形状精度的影响328
6.3.4 工件的安装误差对加工位置精度的影响329
6.3.5 工艺系统的弹性变形对零件加工形状精度的影响329
6.4 影响车削加工表面粗糙度的因素330
6.4.1 影响表面粗糙度的主要因素330
6.4.2 降低表面粗糙度的主要原因331
6.4.3 提高表面粗糙度的有效方法331
6.5 提高车削加工精度的基本途径333
6.5.5 环境方面的基本途径334
6.5.4 工艺方面的基本途径334
6.6 在车床上加工的经济精度334
6.5.2 刀具方面的基本途径334
6.5.3 毛坯方面的基本途径334
6.5.1 机床方面的基本途径334
6.6.1 在车床上加工的尺寸经济精度335
6.6.2 在车床上加工的形状经济精度336
6.6.3 在车床上加工的位置经济精度337
6.6.4 在车床上加工普通与梯形螺纹达到的加工精度338
6.6.5 在车床上加工达到的表面粗糙度范围339
6.7 生产过程及工艺过程341
6.7.1 生产过程与工厂的生产过程341
6.7.2 机械加工工艺过程341
6.7.3 工艺过程对生产的指导、促进、推动作用341
6.7.4 工艺过程的组成与工艺规程的编制342
6.8.1 生产类型的划分343
6.8 生产类型的划分及工序集中与分散的简介343
6.8.2 工序集中与工序分散原则345
6.9 车削步骤正确选择的重要性及其一般原则346
6.9.1 车削步骤正确选择的重要性346
6.9.2 车削步骤正确选择的一般原则346
6.10 车削步骤的选择及其实例348
6.10.1 定位心轴的车削步骤选择348
6.10.2 丝杠的车削步骤选择348
6.10.3 齿轮轴的车削步骤选择349
6.10.4 法兰盘的车削步骤选择350
6.10.5 尾座套筒的车削步骤选择350
6.10.6 车床主轴衬套的车削步骤选择351
7.1.3 基准的定义与其分类353
7.1.2 工件安装的概念353
7.1.1 机械工程图样第1角和第3角画法的简介353
7.1 工件的定位与夹紧及其基准的定义和分类353
第7章 工件装夹的定位原理及车床夹具与其设计程序353
7.2 工件定位基准的选择354
7.2.1 定位粗基准的选择354
7.2.2 定位精基准的选择355
7.3 工件的定位原理及工件的不完全定位、完全定位与过定位356
7.3.1 工件的六点定则356
7.3.2 工件的不完全定位、完全定位与过定位357
7.3.3 车床上常用安装方式的支承点与消除自由度数目的分析357
7.4 工件在夹具上加工误差的分析及尺寸链的换算358
7.4.1 工件在夹具上的定位误差358
7.4.2 工艺尺寸链的换算359
7.5.1 工件以平面定位与其定位元件361
7.5 工件定位基准面的形状及其定位元件361
7.4.3 在夹具上达到工件加工精度的条件361
7.5.2 工件以外圆柱面定位与其定位元件362
7.5.3 工件以圆柱孔定位与其定位元件363
7.5.4 工件以其他形状表面定位与其定位元件364
7.6 夹紧工件的注意事项及防止以摩擦力夹紧方式产生的变形365
7.6.1 夹紧工件的注意事项365
7.6.2 防止以摩擦力方式夹紧工件产生变形的主要方法366
7.7 夹具的用途、分类及其组成367
7.7.1 夹具的用途367
7.7.2 夹具的分类368
7.7.3 夹具的组成369
7.8 车床上常用的特殊顶尖及弹簧拉力心轴与弹簧夹头369
7.8.1 常用特殊顶尖369
7.8.3 弹簧夹头370
7.8.2 弹簧拉力心轴370
7.9 组合夹具的简介及车床用组合夹具的组装371
7.9.1 组合夹具的简介371
7.9.2 组合夹具元件的种类371
7.9.3 车床用组合夹具的组装372
7.9.4 在组合夹具上达到的加工位置精度373
7.10 车床夹具的设计原则及设计程序373
7.10.1 车床夹具的设计原则373
7.10.2 车床夹具的设计程序374
第8章 切削用量、切削液及有屑与无屑加工的余量376
8.1 合理的切削用量选择目的及提高切削用量的途径376
8.1.1 合理切削用量选择目的与其应满足的基本要求376
8.1.2 提高切削用量的主要途径376
8.2.2 切削层横截面要素(物理切削要素)377
8.2.1 切削用量要素(工艺切削要素)377
8.2 车削加工的工艺切削要素及物理切削要素377
8.3 限制切削用量的主要因素及其所限制的程度378
8.3.1 刀具耐用度对切削用量的限制程度378
8.3.2 表面粗糙度对切削用量的限制378
8.3.3 工艺系统刚度对切削用量的限制378
8.3.4 机床切削功率和走刀机构强度对切削用量的限制378
8.4 选择合理切削用量的依据及其原则379
8.4.1 选择合理切削用量的主要依据379
8.4.2 选择合理切削用量的一般原则379
8.5 选择合理切削用量的次序、步骤及其方法380
8.5.1 选择合理切削用量的次序380
8.5.2 选择合理切削用量的步骤381
8.5.3 选择合理切削用量的方法385
8.6 切削液的作用、分类及其添加剂387
8.6.1 切削液的作用387
8.6.2 切削液的分类388
8.6.3 切削液中的添加剂389
8.7 切削液的组成成分及其配方391
8.7.1 切削液的组成成分391
8.7.2 切削液的主要配方392
8.7.3 切削液对切削过程的主要影响393
8.8 切削液的具体选用及其加注方式394
8.8.1 切削液的具体选用394
8.8.2 切削液的加注方式395
8.9 在车床上有屑切削加工的加工余量395
8.9.1 半精车和精车外圆柱面的加工余量395
8.9.2 半精车外圆柱面的磨削加工余量396
8.9.3 钻、扩、半精镗、半精铰为精镗、精铰的加工余量396
8.9.4 半精镗圆柱孔的磨削加工余量397
8.10 在车床上精加工圆柱面及其无屑加工的加工余量398
8.10.1 精镗圆柱孔用钢球或心轴挤扩无屑加工的加工余量398
8.9.6 精车后的研磨与抛光用加工余量398
8.9.5 精车端面的加工余量与半精车端面的磨削加工余量398
8.10.2 精加工圆柱面用滚压工具滚压无屑加工的加工余量399
8.10.3 精车外圆柱面用离心力钢珠冲击无屑加工的加工余量400
第9章 螺纹的切削401
9.1 螺纹的种类、特点与应用及其代号的标记示例401
9.1.1 螺纹的种类、特点与应用401
9.1.2 螺纹的代号标记示例402
9.2 普通螺纹403
9.2.1 普通螺纹的基本牙型403
9.2.2 普通螺纹的公称直径与螺距系列403
9.2.3 普通螺纹的偏差表405
9.2.4 普通螺纹收尾、肩距、退刀槽和倒角424
9.3.2 梯形螺纹的公称直径与螺距系列426
9.3 梯形螺纹426
9.3.1 梯形螺纹的基本牙型与基本牙型尺寸426
9.3.3 梯形螺纹的基本尺寸427
9.3.4 梯形螺纹的公差428
9.3.5 梯形螺纹的极限尺寸432
9.4 管螺纹(圆柱与圆锥管螺纹)米制锥螺纹与60°圆锥螺纹448
9.4.1 用螺纹密封的管螺纹的基本牙型与基本尺寸448
9.4.2 非螺纹密封的管螺纹449
9.4.3 米制锥螺纹基本牙型与基本尺寸452
9.4.4 60°圆锥螺纹的基本牙型与基本尺寸455
9.5 吋制螺纹及非标准方形螺纹455
9.5.1 55°吋制螺纹的基本牙型与基本尺寸455
9.5.2 29°吋制梯形或蜗杆螺纹的基本牙型与基本尺寸456
9.6.1 梯形螺纹刀头的刀尖宽度计算457
9.6 螺纹车刀的刀头尺寸及切削角度的计算457
9.5.3 米制和吋制方形螺纹的牙型与尺寸457
9.6.2 蜗杆螺纹刀头的刀尖宽度计算459
9.6.3 螺纹升角γ对螺纹刀头左、右刃横向工作后角的计算461
9.6.4 螺纹车刀的前角γ0≠0时对螺纹牙型角的影响462
9.6.5 车削阿基米德蜗杆螺纹对螺纹车刀装夹的要求464
9.7 车削螺纹挂轮的计算及挂轮搭配规则465
9.7.1 挂轮计算公式的推导与挂轮搭配规则在单式和复式挂轮系的应用465
9.7.2 无进给箱车床的挂轮计算468
9.7.3 有进给箱车床的新挂轮计算469
9.8 车削螺纹出现乱扣的原因及车削多线螺纹分线的方法471
9.8.1 车削螺纹出现乱扣的原因471
9.8.2 乱扣数的计算471
9.8.3 防止乱扣的方法472
9.8.4 车削多线螺纹分线的方法472
9.8.5 攻螺纹前钻底孔所用钻头直径☆的选择474
9.9 旋风切削螺纹及其工作原理476
9.9.1 旋风切削装置的简介476
9.9.2 旋风切削螺纹的原理、特点与切削方式477
9.9.3 旋风切削螺纹所用刀具材料、刀头切削角度与切削用量478
9.10 螺纹的测量及其主要方法480
9.10.1 用螺纹千分尺测量普通螺纹的中径480
9.10.2 用齿厚游标卡尺测量梯形与蜗杆螺纹的齿厚480
9.10.3 用三针测量法测量螺纹的中径481
第10章 工件加工之中的计算、找正装夹及特殊加工486
10.1 直齿圆柱齿轮坯及斜齿圆柱齿轮坯车削加工的有关计算486
10.1.1 直齿圆柱齿轮坯车削加工的有关计算486
10.1.2 斜齿圆柱齿轮坯车削加工的有关计算486
10.2.1 模数直齿圆锥齿轮坯车削加工的有关计算487
10.2 模数直齿圆锥齿轮坯及径节直齿圆锥齿轮坯车削加工的有关计算487
10.2.2 径节直齿圆锥齿轮坯的车削加工的有关计算488
10.3 普通圆柱蜗杆及蜗轮坏车削加工的有关计算489
10.3.1 模数普通圆柱蜗杆与蜗轮坏车削加工的有关计算489
10.3.2 径节普通圆柱蜗杆与蜗轮坯车削加工的有关计算491
10.4 圆锥面的车削加工及其计算492
10.4.1 圆锥基本参数的名称与符号492
10.4.2 圆锥基本参数的计算公式与斜角近似计算公式的推导493
10.4.3 车削加工圆锥面的方法493
10.4.4 圆锥角度的检测方法499
10.4.5 车削加工圆锥面对背吃刀量和留磨量的控制500
10.4.6 车削加工圆锥面出现双曲线误差的分析502
10.5 奇型工件的划线及其找正装夹503
10.5.1 奇型工件安装常用的附件503
10.5.2 在花盘上安装奇型工件504
10.5.3 在花盘与角铁上用划线找正安装奇型工件505
10.6 偏心工件及曲轴的车削加工506
10.6.1 偏心轴的划线506
10.5.4 减小花盘与角铁定位误差的有效方法506
10.6.2 用床头与尾座上两顶尖支承车削加工偏心轴507
10.6.3 用四爪单动卡盘装夹车削加工偏心件507
10.6.4 用三爪自定心卡盘装夹车削加工偏心件507
10.6.5 用四爪单动卡盘和三爪自定心双重卡盘装夹车削加工偏心件509
10.6.6 双拐与多拐曲轴的车削加工509
10.7 细长轴的车削加工及其装夹方式510
10.7.1 用创新尾座拉力卡头加工细长轴510
10.7.2 用创新尾座拉力卡头与合理切削角度车刀车削加工细长轴511
10.7.3 用创新尾座拉力卡头与三支承块跟刀架车削加工细长轴511
10.8 深孔的加工及套料加工512
10.8.1 深孔钻的结构形式与几何形状512
10.7.4 用创新尾座拉力卡头、三支承块跟刀架与改变走刀方向车削加工细长轴512
10.8.2 枪孔钻的结构形式与几何形状514
10.8.3 双刃错齿内排屑深孔钻主要参数的确定515
10.8.4 深孔钻削加工的切削用量与其注意事项517
10.8.5 深孔的套料加工517
10.9 精密球面及特种形面的车削加工519
10.9.1 用球面装置车削加工精密球面519
10.9.2 用靠模法车削加工凸轮520
10.9.3 用样件作靠模车削加工特种形面的环状槽521
10.10 用专用装置车削加工多边形体及其平面度误差分析522
10.10.1 多边形体的车削加工原理522
10.10.2 外切法车削加工多边形体专用装置的简介523
10.10.3 车削加工多边形体的具体操作要求523
10.10.4 车削加工多边形体平面度误差的分析524
参考文献526
热门推荐
- 928934.html
- 2761796.html
- 2124876.html
- 2041943.html
- 3037151.html
- 1803231.html
- 1142477.html
- 354134.html
- 377443.html
- 3535156.html
- http://www.ickdjs.cc/book_2605899.html
- http://www.ickdjs.cc/book_3393047.html
- http://www.ickdjs.cc/book_3817028.html
- http://www.ickdjs.cc/book_2140464.html
- http://www.ickdjs.cc/book_277763.html
- http://www.ickdjs.cc/book_3491501.html
- http://www.ickdjs.cc/book_818391.html
- http://www.ickdjs.cc/book_2018795.html
- http://www.ickdjs.cc/book_98003.html
- http://www.ickdjs.cc/book_872417.html