图书介绍
统计过程控制理论与实践 SPC、Cpk、DOE、MSA、PPM技术【2025|PDF|Epub|mobi|kindle电子书版本百度云盘下载】
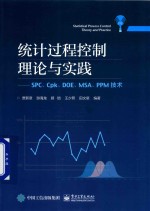
- 贾新章,游海龙,田文星等编著 著
- 出版社: 北京:电子工业出版社
- ISBN:9787121329739
- 出版时间:2017
- 标注页数:322页
- 文件大小:50MB
- 文件页数:338页
- 主题词:统计控制-过程控制-高等学校-教材
PDF下载
下载说明
统计过程控制理论与实践 SPC、Cpk、DOE、MSA、PPM技术PDF格式电子书版下载
下载的文件为RAR压缩包。需要使用解压软件进行解压得到PDF格式图书。建议使用BT下载工具Free Download Manager进行下载,简称FDM(免费,没有广告,支持多平台)。本站资源全部打包为BT种子。所以需要使用专业的BT下载软件进行下载。如BitComet qBittorrent uTorrent等BT下载工具。迅雷目前由于本站不是热门资源。不推荐使用!后期资源热门了。安装了迅雷也可以迅雷进行下载!
(文件页数 要大于 标注页数,上中下等多册电子书除外)
注意:本站所有压缩包均有解压码: 点击下载压缩包解压工具
图书目录
第1章 概论1
1.1 关于产品质量可靠性的基本理念1
1.1.1 保证、评价产品质量可靠性常规方法存在的问题1
1.1.2 关于质量可靠性的基本理念6
1.1.3 保证和评价产品质量可靠性的相关技术8
1.2 生产过程统计质量控制的技术流程8
1.2.1 制造过程对参数一致性和稳定性的影响8
1.2.2 统计过程控制的目的和相关技术9
1.2.3 实施质量控制的技术流程10
1.2.4 实施SPC的基本条件12
思考题与习题13
第2章 工序能力指数与6σ设计14
2.1 预备知识——工艺参数分布规律的定量描述14
2.1.1 正态分布函数14
2.1.2 正态分布特征值的统计特性19
2.2 工序能力的定量表征和工序能力指数21
2.2.1 工艺参数一致性与工序能力21
2.2.2 工序能力指数(Cp)22
2.2.3 实际工序能力指数(Cpk)23
2.2.4 工业生产对工序能力指数的要求26
2.3 工序能力指数的计算26
2.3.1 均值(μ)和标准偏差(σ)的计算方法26
2.3.2 工序能力指数计算实例27
2.4 6σ设计与等效工序能力指数28
2.4.1 从工序能力指数理解6σ设计的含义和目标28
2.4.2 pσ设计水平与DPMO29
2.4.3 基于6σ设计理念的ECpk31
2.4.4 ECpk计算中涉及的两个算法32
思考题与习题33
第3章 工序能力指数评价的特殊模型36
3.1 工序能力指数常规计算方法的适用条件36
3.2 非正态分布工艺参数的工序能力指数计算方法37
3.2.1 非正态分布工艺参数数据37
3.2.2 计算方法一:基于数据转换的计算方法38
3.2.3 计算方法二:基于工艺成品率的计算方法40
3.2.4 非正态分布参数工序能力指数计算方法讨论41
3.3 多参数情况工序能力指数计算方法43
3.3.1 多变量工序能力指数MCpk计算思路43
3.3.2 MCpk计算步骤44
3.3.3 MCpk应用实例45
3.3.4 多元正态分布函数的高精度积分算法47
3.4 计件值工序能力指数47
3.4.1 描述计件值数据分布规律的二项分布48
3.4.2 计件值工序能力指数的计算思路49
3.4.3 计件值工序能力指数计算方法一:每批样本量相同50
3.4.4 计件值工序能力指数计算方法二:每批样本量不相同53
3.5 计点值工序能力指数55
3.5.1 描述计点值数据分布规律的泊松分布55
3.5.2 计点值工序能力指数的计算思路56
3.5.3 计点值工序能力指数计算方法一:每批样本量相同56
3.5.4 计点值工序能力指数计算方法二:每批样本量不相同59
思考题与习题61
第4章 统计过程控制与常规控制图62
4.1 SPC与控制图62
4.1.1 SPC基本概念62
4.1.2 “统计受控”与“加工结果是否合格”的关系64
4.1.3 控制图的结构和作用66
4.1.4 控制限的计算原理68
4.1.5 工艺过程受控/失控状态的判断规则68
4.1.6 常规控制图的分类70
4.2 常规计量值控制图71
4.2.1 “均值—标准偏差”控制图71
4.2.2 “均值—极差”控制图75
4.2.3 “单值—移动极差”控制图78
4.3 常规计件值控制图80
4.3.1 不合格品数控制图(np图)81
4.3.2 不合格品率控制图(p图)82
4.3.3 通用不合格品率控制图(pT图)85
4.4 常规计点值控制图87
4.4.1 缺陷数控制图(c图)87
4.4.2 单位缺陷数控制图(u图)88
4.4.3 通用单位缺陷数控制图(uT图)91
4.5 常规控制图的应用92
4.5.1 关于“分析用控制图”与“控制用控制图”92
4.5.2 常规计量值控制图应用实例93
4.5.3 常规计数值控制图应用实例98
思考题与习题105
第5章 特殊控制图107
5.1 特殊控制图的基本原理107
5.1.1 常规控制图的适用条件107
5.1.2 需要采用特殊控制图的典型情况108
5.1.3 特殊控制图的基本原理112
5.2 适用于非正态分布数据的控制图112
5.2.1 非正态分布数据的控制图分析方法112
5.2.2 制造过程非正态分布数据控制图实例113
5.2.3 非制造过程中非正态分布数据控制图实例113
5.3 适用于多品种情况的回归控制图118
5.3.1 回归控制图原理118
5.3.2 回归方法一:标准正态处理方法与应用118
5.3.3 回归方法二:“相对偏差”方法与应用120
5.3.4 关于“双重回归”情况123
5.3.5 对多品种情况的一种不正确处理方法124
5.4 适用于多品种小批量情况的T-K控制图125
5.4.1 T统计量与T控制图125
5.4.2 K统计量与K控制图127
5.4.3 T-K控制图的特点128
5.4.4 T-K控制图应用实例128
5.5 适用于批加工参数的嵌套控制图131
5.5.1 “批加工”生产特点与参数的嵌套性131
5.5.2 工艺参数数据的嵌套性检验134
5.5.3 一阶嵌套控制图模型与应用136
5.5.4 二阶嵌套控制图模型与应用137
5.6 适用于多参数情况的多变量控制图142
5.6.1 多参数问题与多变量控制图143
5.6.2 多变量T2控制图144
5.6.3 单值多变量T2控制图148
5.6.4 多变量控制图的应用实例149
5.6.5 针对多参数问题的一种不正确处理方法153
5.7 综合控制图154
5.7.1 关于综合控制图154
5.7.2 综合控制图应用实例154
5.8 分位数控制图158
5.8.1 分位数控制图的原理158
5.8.2 计点值分位数控制图160
5.8.3 计件值分位数控制图163
5.8.4 适用于非正态计量值的分位数控制图165
5.9 缺陷成团控制图170
5.9.1 缺陷成团模型170
5.9.2 缺陷成团控制图171
5.9.3 缺陷成团控制图应用实例172
思考题与习题174
第6章 Cpk和SPC应用实践176
6.1 工序能力指数评价实施方案的制订176
6.1.1 Cpk评价流程和实施方案的制订要求176
6.1.2 关键工序过程节点与关键工艺参数177
6.1.3 用于Cpk评价的数据采集178
6.1.4 工序能力指数计算180
6.2 提升Cpk的技术途径182
6.2.1 提升工序能力指数的技术途径182
6.2.2 工序能力指数提升实例184
6.3 SPC实施方案的制订187
6.3.1 SPC实施方案的制订要求187
6.3.2 用于SPC评价的数据采集188
6.3.3 控制图的正确选用189
6.4 失控问题分析192
6.4.1 失控问题分析的基本思路192
6.4.2 控制图综合应用分析实例1194
6.4.3 控制图综合应用分析实例2197
6.4.4 控制图综合应用分析实例3202
思考题与习题206
第7章 过程改进工具——DOE技术207
7.1 DOE的含义与作用207
7.1.1 引例——PCB挖槽工艺的优化207
7.1.2 什么是试验设计209
7.1.3 试验设计中基本术语210
7.1.4 符号化与效应计算212
7.1.5 试验设计的作用215
7.2 试验设计的基本步骤与关键技术216
7.2.1 试验设计的基本步骤216
7.2.2 步骤1:明确试验目的、确定表征对象217
7.2.3 步骤2:确定影响表征对象的因素及其变化范围218
7.2.4 步骤3:选择试验类型、制订试验方案219
7.2.5 步骤4:实施试验、采集数据221
7.2.6 步骤5:数据分析222
7.2.7 步骤6:基于表征模型实现过程的控制与优化222
7.2.8 步骤7:结论与建议222
7.2.9 试验设计类型223
7.2.10 试验设计数据分析方法224
7.3 方差分析226
7.3.1 一个示例——方差分析的作用226
7.3.2 单因素试验的方差分析228
7.3.3 多因素试验的方差分析230
7.3.4 方差分析的基本假设237
7.3.5 数据转换237
7.4 回归分析239
7.4.1 回归分析的基本概念240
7.4.2 一元线性回归240
7.4.3 一元非线性回归244
7.5 两水平全因子试验设计247
7.5.1 因子试验设计与两水平因子设计247
7.5.2 两水平全因子试验设计实例——外延层生长工艺248
7.5.3 基于模型的优化策略——晶体外延层生长工艺的优化255
7.5.4 讨论——试验类型的选取257
7.6 试验设计应用实例与分析259
7.6.1 微电路热氧化工艺的表征与优化259
7.6.2 基于D最优化的等离子刻蚀工艺的表征与优化267
思考题与习题275
第8章 常用的统计分析工具277
8.1 直方图277
8.1.1 直方图的含义与作用277
8.1.2 直方图的绘制步骤278
8.1.3 直方图的使用278
8.2 概率纸280
8.2.1 什么是概率纸280
8.2.2 正态概率纸281
8.2.3 对数正态概率纸应用实例282
8.3 箱线图283
8.3.1 箱线图的构成283
8.3.2 箱线图的应用284
8.4 检查表和分层法284
8.4.1 检查表285
8.4.2 分层法286
8.5 Pareto图286
8.5.1 Pareto图的基本构成286
8.5.2 Pareto图的其他应用方式287
8.6 因果分析图288
8.6.1 因果分析图的构成288
8.6.2 因果分析图的绘制步骤289
8.7 散点图290
8.7.1 散点图的构成290
8.7.2 散点图上显示的相关关系290
思考题与习题291
第9章 MSA与测量仪器精密度评价292
9.1 测量仪器评价的相关概念和基本要求292
9.1.1 测量仪器评价的相关概念292
9.1.2 测量仪器评价的基本要求294
9.2 测量仪器精密度和分辨力对SPC评价结果的影响295
9.2.1 仪器精密度对工序能力指数评价结果的影响295
9.2.2 仪器分辨力对参数分布评价结果的影响296
9.2.3 仪器分辨力对SPC评价结果的影响296
9.2.4 仪器精密度对产品合格与否评价结果的影响297
9.2.5 测量仪器精密度的评价流程299
9.3 测量仪器精密度评价的步骤299
9.3.1 步骤1—数据采集300
9.3.2 步骤2—统计受控状态的评价301
9.3.3 步骤3—“重复性”的评价304
9.3.4 步骤4—“再现性”的评价305
9.3.5 步骤5—“精密度”的评价306
9.3.6 步骤6—计算总的标准偏差σ总306
9.3.7 步骤7—σ仪器与σ总之比的评价308
9.4 仪器精密度评价实例310
思考题与习题315
第10章 出厂产品不合格水平PPM评价316
10.1 PPM评价的概念和要求316
10.1.1 PPM评价的基本原理316
10.1.2 PPM评价数据的采集途径317
10.2 产品出厂平均质量水平的评定318
10.2.1 PPM分类318
10.2.2 PPM计算方法一318
10.2.3 PPM计算方法二320
思考题与习题321
参考资料322
热门推荐
- 1671350.html
- 516771.html
- 1513950.html
- 1872888.html
- 3205254.html
- 2370010.html
- 1332435.html
- 3340427.html
- 3339411.html
- 3557282.html
- http://www.ickdjs.cc/book_163282.html
- http://www.ickdjs.cc/book_3472797.html
- http://www.ickdjs.cc/book_1682157.html
- http://www.ickdjs.cc/book_3166953.html
- http://www.ickdjs.cc/book_1738574.html
- http://www.ickdjs.cc/book_1428323.html
- http://www.ickdjs.cc/book_250408.html
- http://www.ickdjs.cc/book_2677453.html
- http://www.ickdjs.cc/book_3123250.html
- http://www.ickdjs.cc/book_1151355.html