图书介绍
车削工艺技术【2025|PDF|Epub|mobi|kindle电子书版本百度云盘下载】
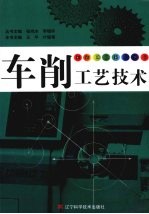
- 王平,叶晓苇本书主编 著
- 出版社: 沈阳:辽宁科学技术出版社
- ISBN:9787538156348
- 出版时间:2009
- 标注页数:416页
- 文件大小:18MB
- 文件页数:432页
- 主题词:车削-工艺
PDF下载
下载说明
车削工艺技术PDF格式电子书版下载
下载的文件为RAR压缩包。需要使用解压软件进行解压得到PDF格式图书。建议使用BT下载工具Free Download Manager进行下载,简称FDM(免费,没有广告,支持多平台)。本站资源全部打包为BT种子。所以需要使用专业的BT下载软件进行下载。如BitComet qBittorrent uTorrent等BT下载工具。迅雷目前由于本站不是热门资源。不推荐使用!后期资源热门了。安装了迅雷也可以迅雷进行下载!
(文件页数 要大于 标注页数,上中下等多册电子书除外)
注意:本站所有压缩包均有解压码: 点击下载压缩包解压工具
图书目录
第一章 车床1
1.1 机床的型号1
1.1.1 机床型号的表示1
1.1.2 机床型号的编制1
1.1.3 车削加工的特点4
1.2 车床的分类及结构5
1.2.1 车床的分类5
1.2.2 普通车床的结构组成7
1.3 CA6140普通卧式车床8
1.3.1 CA6140车床的传动系统8
1.3.2 CA6140车床主要部件的结构14
1.4 车床精度及其调整17
1.4.1 车床精度的检测17
1.4.2 车床精度的调整22
1.5 车床的维护保养26
1.5.1 车床一级保养的内容26
1.5.2 车床的二级保养26
1.5.3 车床的合理润滑27
第二章 切削基本原理29
2.1 切削运动、工件上的加工表面、切削用量与材料切除率29
2.1.1 切削运动29
2.1.2 工件上的加工表面29
2.1.3 切削用量和材料切除率30
2.2 切削过程与切屑类型30
2.2.1 切削过程30
2.2.2 切屑类型31
2.3 积屑瘤32
2.3.1 积屑瘤对加工的影响32
2.3.2 积屑瘤的形成及防止33
2.4 切削力及切削热33
2.4.1 切削力33
2.4.2 切削热与切削温度35
2.4.3 刀具的磨损与刀具寿命37
2.5 刀具切削部分38
2.5.1 刀具切削部分的组成39
2.5.2 确定刀具角度的三个辅助平面39
2.5.3 车刀的切削角度及其作用40
2.5.4 车刀切削角度的合理选择41
2.6 切削用量的选择46
2.6.1 切削用量选择的一般原则46
2.6.2 不同切削条件下选择切削用量的几点原则47
2.7 切削液及其合理选用47
2.7.1 切削液的作用47
2.7.2 切削液的种类48
2.7.3 切削液的选用和使用注意事项48
第三章 车床用刀具49
3.1 刀具材料49
3.1.1 高速钢49
3.1.2 硬质合金刀具材料50
3.1.3 其他常用车刀材料52
3.2 车刀的种类及结构55
3.2.1 车刀的种类55
3.3 车刀的刃磨72
3.3.1 车刀的磨钝标准72
3.3.2 车刀的刃磨73
3.3.3 车刀角度的测量76
3.4 孔加工刀具76
3.4.1 孔加工刀具的种类和用途76
3.4.2 标准麻花钻77
3.4.3 群钻80
3.4.4 扩孔钻82
3.4.5 锪钻82
3.4.6 铰刀83
第四章 车床夹具和辅具85
4.1 定位85
4.1.1 定位和基准85
4.1.2 六点定位原理86
4.1.3 工件的定位方法和定位元件88
4.2 工件的夹紧91
4.2.1 工件夹紧的基本原则91
4.2.2 工件的夹紧方法和夹紧装置92
4.3 车床典型夹具95
4.3.1 车削夹具的分类和用途95
4.3.2 通用夹具的结构95
4.3.3 组合夹具101
第五章 车削常用量具103
5.1 游标读数量具103
5.1.1 游标卡尺103
5.1.2 深度游标卡尺和高度游标卡尺104
5.1.3 游标万能角度尺105
5.1.4 齿厚游标尺106
5.2 带表尺和数显尺107
5.2.1 带表卡尺和数显卡尺107
5.2.2 圆标高度尺和数显高度尺107
5.3 测微量具108
5.3.1 外径千分尺108
5.3.2 内径千分尺110
5.3.3 深度千分尺110
5.3.4 螺纹千分尺110
5.3 指示式量具111
5.4.1 钟面式百分表111
5.4.2 杠杆式百分表113
5.5 水平仪114
第六章 轴类零件的车削116
6.1 轴类零件的特点与技术要求116
6.1.1 轴类零件的结构特点116
6.1.2 轴类零件的技术要求116
6.1.3 材料与热处理117
6.1.4 毛坯选择117
6.2 轴类零件的装夹117
6.2.1 用三爪自定心卡盘装夹工件118
6.2.2 用四爪单动卡盘装夹工件118
6.2.3 用“双顶尖”装夹工件118
6.2.4 用“一夹一顶”法装夹工件123
6.2.5 中心架和跟刀架的使用124
6.2.6 花盘安装124
6.3 车削加工124
6.3.1 车外圆124
6.3.2 车端面126
6.3.3 车台阶127
6.3.4 切槽及切断加工128
6.3.5 轴类零件的检测133
6.4 车削加工经济精度与表面粗糙度134
6.4.1 车削加工的工艺特点134
6.4.2 车削加工的经济精度与表面粗糙度134
6.5 轴类零件车削实例139
6.5.1 结构工艺及技术要求分析139
6.5.2 卧式车床主轴车削加工工艺方案141
6.6 外圆车削加工中常见质量问题及防止措施145
6.6.1 车床精度对加工质量的影响及消除方法145
6.6.2 高精度工件车削车床的调整147
6.6.3 强力车削车床的调整148
第七章 盘套类零件的车削149
7.1 盘套类零件的结构及一般技术要求149
7.1.1 钻孔149
7.1.2 扩孔151
7.1.3 铰孔151
7.1.4 镗孔152
7.2 内孔的车削加工152
7.2.1 刀具的安装152
7.2.2 钻孔153
7.2.3 扩孔和锪孔155
7.2.4 镗孔(车孔)156
7.2.5 内沟槽的车削157
7.2.6 铰孔158
7.3 盘套类零件的装夹162
7.3.1 薄壁工件的装夹162
7.3.2 保证内外圆位置精度要求的装夹163
7.4 盘套类零件的检测167
7.4.1 尺寸精度检验167
7.4.2 几何形状精度检验169
7.4.3 相互位置精度检验169
7.5 盘套类零件车削实例171
7.6 内孔加工常见质量问题及防止措施172
7.6.1 钻孔时常见的质量问题172
7.6.2 扩孔时常见的质量问题174
7.6.3 镗孔(车孔)时常见的质量问题175
7.6.4 铰孔时常见的质量问题177
第八章 圆锥面的车削181
8.1 圆锥面的基本参数181
8.1.1 圆锥面的主要尺寸181
8.1.2 圆锥各部分尺寸计算181
8.1.3 常用的标准圆锥182
8.2 外锥面的车削加工183
8.2.1 转动小刀架法184
8.2.2 偏移尾座法186
8.2.3 仿形法(靠模法)188
8.2.4 宽刃刀车削法189
8.3 内锥面的车削加工189
8.3.1 转动小刀架法190
8.3.2 仿形法190
8.3.3 铰内圆锥190
8.4 圆锥尺寸的控制方法191
8.4.1 计算法192
8.4.2 移动大拖板法192
8.5 圆锥面的检测193
8.5.1 角度(或锥度)的检验193
8.5.2 圆锥的尺寸检验195
8.6 圆锥面车削加工实例196
8.7 圆锥面车削常见质量问题及防止措施197
8.7.1 锥度不正确197
8.7.2 圆锥母线不直(双曲线误差)198
8.7.3 圆锥面大、小端尺寸不正确199
第九章 成形面的车削200
9.1 用合成运动法车削成形面200
9.2 用成形刀法车削成形面202
9.2.1 成形刀的种类202
9.2.2 成形刀的选择原则204
9.3 用仿形法车削成形面205
9.3.1 用仿形车床车削成形面205
9.3.2 用床身靠模法车削成形面206
9.3.3 用尾座靠模法车削成形面206
9.3.4 用横向靠模法车削成形面207
9.4 用专用工具车削成形面208
9.4.1 手动车内外圆弧工具208
9.4.2 蜗杆副车内外圆弧工具209
9.4.3 用旋风切削法车削圆球面209
9.4.4 成形面的检验211
9.5 成形面车削加工应注意的问题212
9.5.1 用仿形车床车削成形面的允许角度212
9.5.2 用仿形车床车削内形面的允许角度213
9.5.3 仿形车削时车刀主、副偏角213
9.5.4 内仿形车削时车刀主、副偏角214
9.6 成形面仿形车削常见质量问题及防止措施215
9.6.1 仿形车削时外圆锥度215
9.6.2 仿形车削阶梯轴215
9.6.3 仿形车削时,工件的轴向尺寸215
9.6.4 仿形车削时的倒角216
9.6.5 仿形车削时,圆弧半径扩大216
第十章 螺纹的车削217
10.1 螺纹车刀及其安装217
10.1.1 螺纹车刀几何形状要求217
10.1.2 螺纹车刀的装夹217
10.2 三角形螺纹的车削218
10.2.1 螺纹车削进刀方式219
10.2.2 低速车削三角形螺纹220
10.2.3 高速车削三角形螺纹220
10.2.4 螺纹车削时的安全知识221
10.3 交换齿轮的计算和调整222
10.3.1 交换齿轮计算公式222
10.3.2 交换齿轮啮合规则223
10.3.3 交换齿轮计算224
10.3.4 交换齿轮组装注意事项225
10.4 乱牙和预防方法226
10.4.1 产生乱牙的原因226
10.4.2 预防乱牙的方法226
10.5 用板牙和丝锥切削螺纹226
10.5.1 用板牙套螺纹227
10.5.2 用丝锥攻螺纹227
10.6 矩形螺纹车削228
10.6.1 矩形螺纹的牙型和基本尺寸计算229
10.6.2 矩形螺纹车刀229
10.6.3 矩形螺纹的车削方法230
10.7 梯形螺纹车削230
10.7.1 梯形螺纹的标记230
10.7.2 梯形螺纹的尺寸计算231
10.7.3 梯形螺纹车刀232
10.7.4 梯形外螺纹的车削233
10.7.5 梯形内螺纹的加工方法234
10.8 蜗杆的车削236
10.8.1 蜗杆各部分尺寸计算236
10.8.2 车削蜗杆时交换齿轮计算238
10.8.3 蜗杆车刀238
10.8.4 蜗杆的车削方法240
10.9 多线螺纹的车削241
10.9.1 多线螺纹车削时交换齿轮计算241
10.9.2 多线螺纹车削时的分线方法241
10.9.3 多线螺纹的车削步骤243
10.10 螺纹的测量243
10.10.1 综合测量244
10.10.2 单项测量244
10.11 螺纹加工产生废品及质量问题的原因及防止措施247
10.11.1 车削螺纹时产生废品的原因及防止措施247
10.11.2 攻螺纹和套螺纹时产生废品的原因及防止措施248
10.11.3 不同的螺纹形状应选择不同的螺纹车削方法248
10.11.4 螺纹车削常见质量问题及防止措施250
第十一章 复杂、精密零件的车削254
11.1 在花盘角铁上加工工件254
11.1.1 基准面的选择254
11.1.2 花盘与角铁的一般使用方法259
11.1.3 在花盘上车削工件261
11.1.4 在角铁上加工工件263
11.1.5 花盘角铁上保证形位公差、中心距要求的方法265
11.2 细长轴车削265
11.2.1 细长轴的结构与工艺特点266
11.2.2 中心架的使用方法266
11.2.3 跟刀架的使用方法267
11.2.4 细长轴的车削267
11.2.5 细长轴车削常见问题及防止措施270
11.3 偏心件和曲轴车削274
11.3.1 偏心工件的划线方法274
11.3.2 在四爪单动卡盘上车削偏心工件275
11.3.3 在花盘上车削偏心孔工件276
11.3.4 在两顶尖间车削偏心工件276
11.3.5 在三爪自定心卡盘上车削偏心工件276
11.3.6 用双卡盘车削偏心工件277
11.3.7 用偏心卡盘车削偏心工件277
11.3.8 在专用夹具上车削偏心工件278
11.3.9 在通用可调整夹具中车削偏心工件279
11.3.10 偏心距的测量方法279
11.3.11 曲轴的车削方法281
11.4 深孔加工282
11.4.1 深孔加工排屑方式282
11.4.2 深孔加工的方法284
11.5 丝杠车削287
11.5.1 丝杠螺纹车刀288
11.5.2 丝杠螺纹的车削288
11.5.3 螺距误差校正装置288
11.5.4 丝杠螺距精度的测量288
11.6 复杂、精密零件车削加工实例289
11.6.1 丝杠的车削289
11.6.2 多拐曲轴的车削294
第十二章 难加工材料的车削303
12.1 影响材料切削加工特性的因素303
12.1.1 材料的化学成分303
12.1.2 材料的物理性能303
12.1.3 材料的力学性能304
12.1.4 难切削材料的切削特点304
12.2 常见难加工材料的车削305
12.2.1 高强度及超高强度钢的车削305
12.2.2 高锰钢的车削306
12.2.3 淬硬钢、冷硬铸铁及耐磨合金铸铁的车削308
12.2.4 不锈钢、高温合金的车削310
12.2.5 橡胶、工程塑料及复合材料的车削314
第十三章 数控车削加工基础317
13.1 数控机床317
13.1.1 数控机床的特点317
13.1.2 数控机床的工作原理及组成319
13.1.3 数控机床的分类320
13.1.4 数控车床的保养322
13.1.5 数控车床的安全操作规程323
13.2 数控车削编程324
13.2.1 数控车削的编程特点324
13.2.2 车床数控系统的功能与指令代码325
13.2.3 数控车削编程中的有关问题327
13.3 数控车床基本指令编程329
13.3.1 尺寸坐标系统329
13.3.2 刀具功能T、主轴转速功能S和进给功能F331
13.3.3 常用的辅助功能332
13.3.4 插补指令编程333
13.3.5 螺纹车削加工指令(G32/G33)334
13.3.6 刀具补偿指令(G41、G42、G40)336
13.3.7 固定循环.337
13.4 编程实例340
13.4.1 实例1340
13.4.2 实例2341
第十四章 华中(HNC—21/22T)车床数控系统343
14.1 零件程序的结构343
14.1.1 坐标系统343
14.1.2 指令字的格式344
14.1.3 程序的一般结构345
14.2 HNC—21/22T数控系统的编程指令体系345
14.2.1 辅助功能M指令代码345
14.2.2 主轴功能S、进给功能F和刀具功能T348
14.2.3 准备功能G指令代码349
14.3 综合编程实例377
第十五章 FANUC0i—TA车床数控系统379
15.1 加工程序的结构379
15.1.1 加工程序的组成379
15.1.2 加工程序的格式379
15.1.3 主要地址和指令值范围380
15.2 坐标系381
15.2.1 机床坐标系381
15.2.2 工件坐标系382
15.2.3 平面选择386
15.3 FANUC0i—TA数控系统的编程指令体系387
15.3.1 准备功能G指令387
15.3.2 辅助功能M指令389
15.3.3 F、T、S功能391
15.4 FANUC0i—TA数控系统的基本编程指令394
15.4.1 绝对值和增量值编程(G90、G91)394
15.4.2 英制/米制转换(G20、G21)394
15.4.3 插补功能395
15.5 典型零件编程加工实例408
附录411
附录1 车削加工通用工艺守则411
附录2 车床安全操作规程413
附录3 蜗杆导程角γ0、量针测量距M值414
参考文献416
热门推荐
- 1602506.html
- 3673602.html
- 3374295.html
- 3308706.html
- 3613692.html
- 1353885.html
- 315514.html
- 3815367.html
- 2223557.html
- 2839103.html
- http://www.ickdjs.cc/book_1857887.html
- http://www.ickdjs.cc/book_1716596.html
- http://www.ickdjs.cc/book_805285.html
- http://www.ickdjs.cc/book_3850251.html
- http://www.ickdjs.cc/book_3069601.html
- http://www.ickdjs.cc/book_416780.html
- http://www.ickdjs.cc/book_2808019.html
- http://www.ickdjs.cc/book_2418717.html
- http://www.ickdjs.cc/book_1505329.html
- http://www.ickdjs.cc/book_1404022.html